Over the last few years I have written a fair bit about carving Finnish Candles or Log Rockets using just the tools I would carry in my bergen (saws, knives, axes etc) so I thought it was time to see what could be done with a chainsaw.
I decided to opt for the Log Rocket as I thought there has been plenty written about using Finnish Candles (referred to sometimes as Swedish Candles/Torches). At the Bushcraft UK Bushmoot last year I asked my friend Rob Nash if he was willing to carve a large log rocket for me using his chainsaw.
For those of you who just like to watch a short video on its construction here it is – for those of you who prefer detailed instructions there are loads of pictorial steps after the video below.
The Log Rocket
The log rocket worked spectacularly and you can get a sense of scale (forgot to measure it) from the picture of Rob standing next to it.
I chose a large piece of piece of what I think was Spruce (hard to tell when there is no bark and it is seasoned). I will be referring to the 3 parts of the log rocket as you can see in the bottom left picture below.
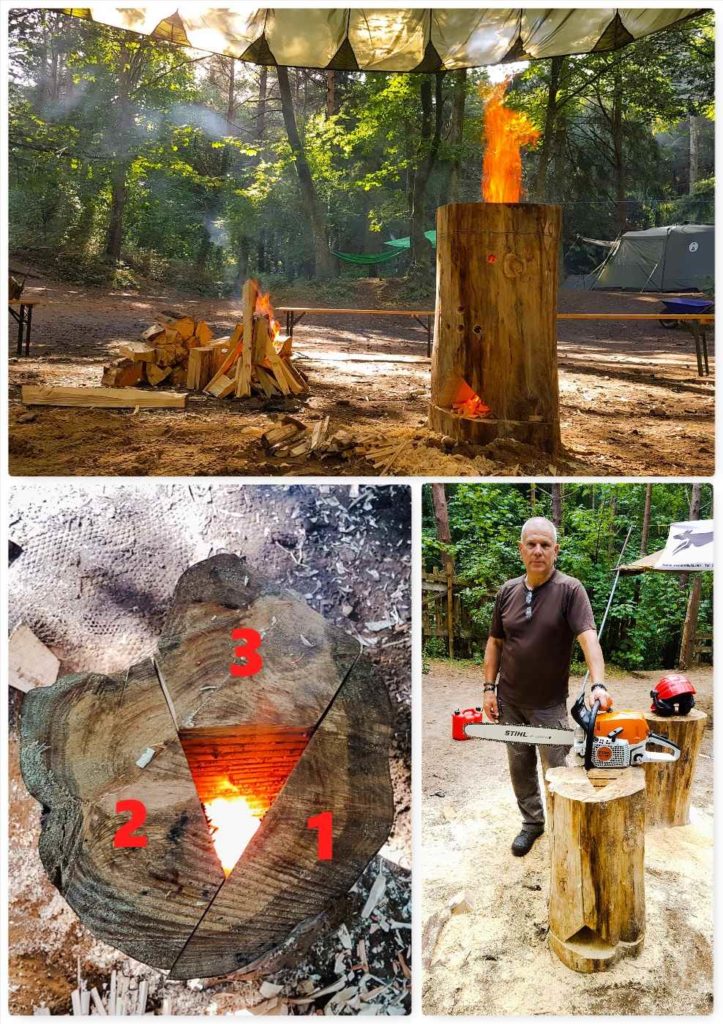
Section 1
Rob took out a slice of the log (approx 1/3 of the log) and stopped the cut about 15 cms from the bottom. Then he cut in from the side at the bottom of the log to remove Section 1.
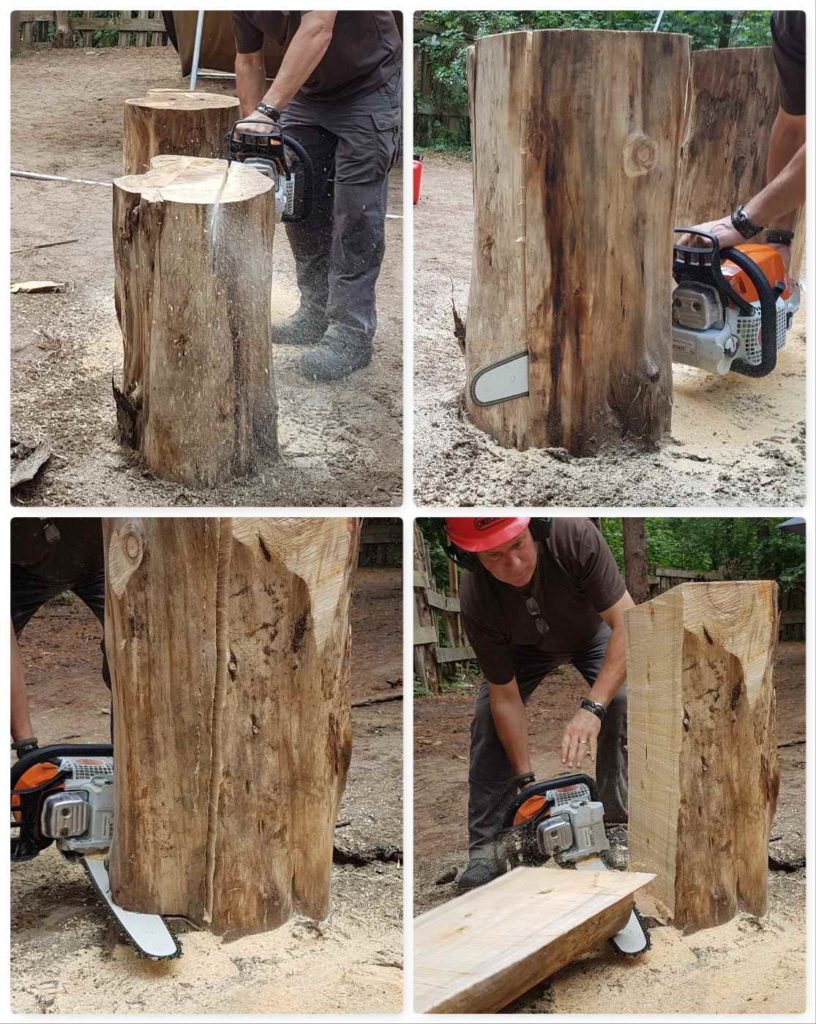
Section 2
To describe this cut is quite difficult so refer to the picture above in which the pieces are numbered. The aim was to leave Section 3 with a point that could be removed to form the chimney. Again it was a case of cutting down to about 15 cms from the bottom and removing section 2 by cutting in from the side.
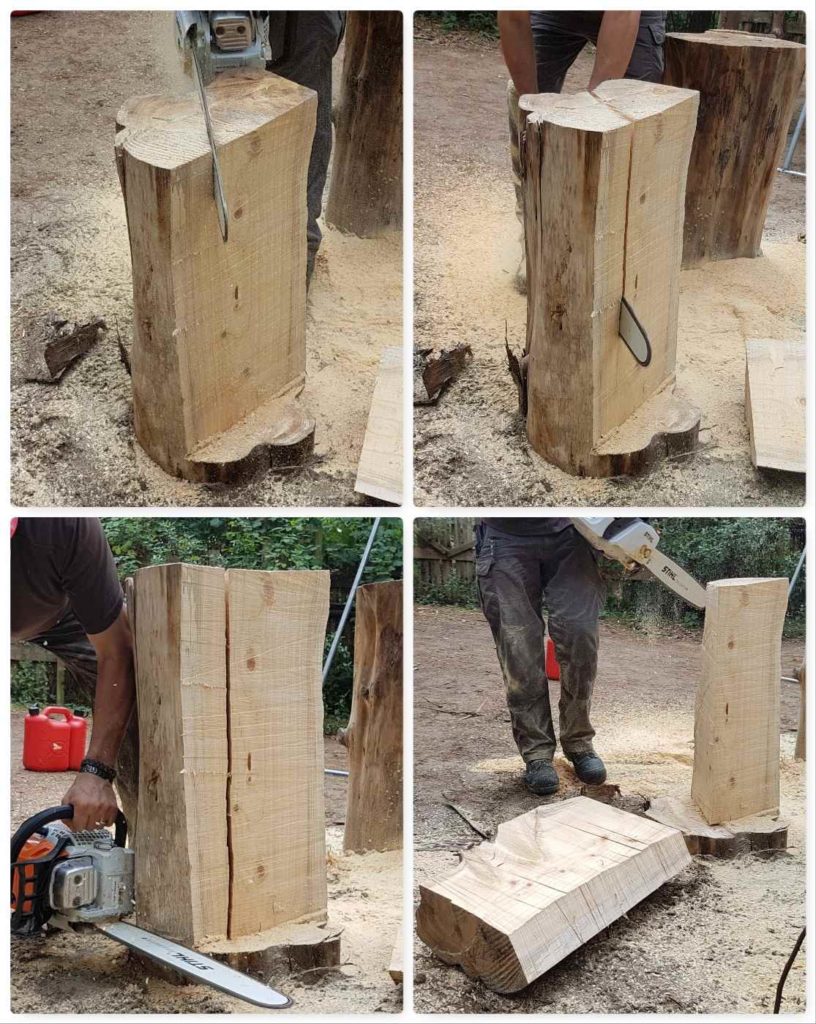
Section 3
You can clearly see the point left on Section 3. Rob made an undercut at the bottom first this time and then removed the ‘Point’. This is the area that would form the chimney. The triangular-shaped piece of wood from the centre point was split down further with an axe to form the kindling to get the log rocket going.
The final step here in the bottom right picture shows Rob cutting out a piece of wood at the bottom of Section 3 to slightly enlarge the ‘firebox’ area.
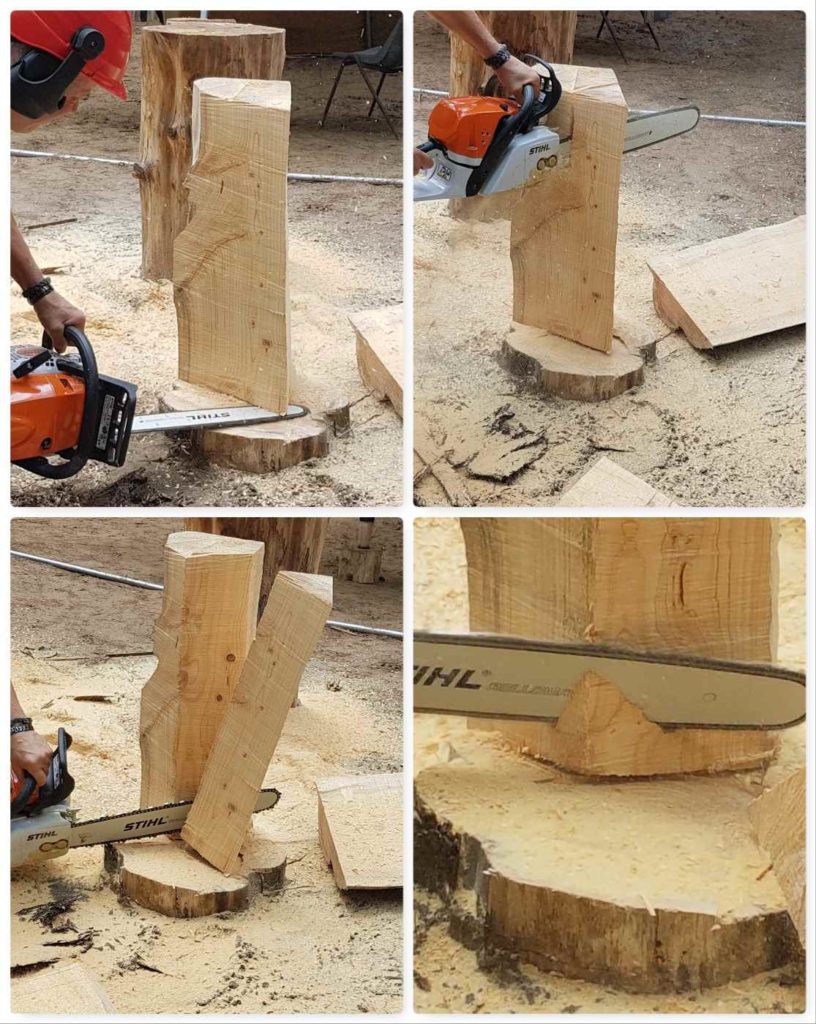
Firebox opening
I have shown the final look of the firebox opening in the top left picture below. Rob created this firstly by re-assembling Sections 1 & 2 with Section 3. The he marked the corners of Sections 1 & 2 that needed cutting to form the firebox opening (that might sound overly complicated, but it’s important if you’re not to cut the wrong corners).
Once he’d cut off the corners he shaved off more wood from the ‘Shoulder’ of the opening so as to enlarge the firebox area.
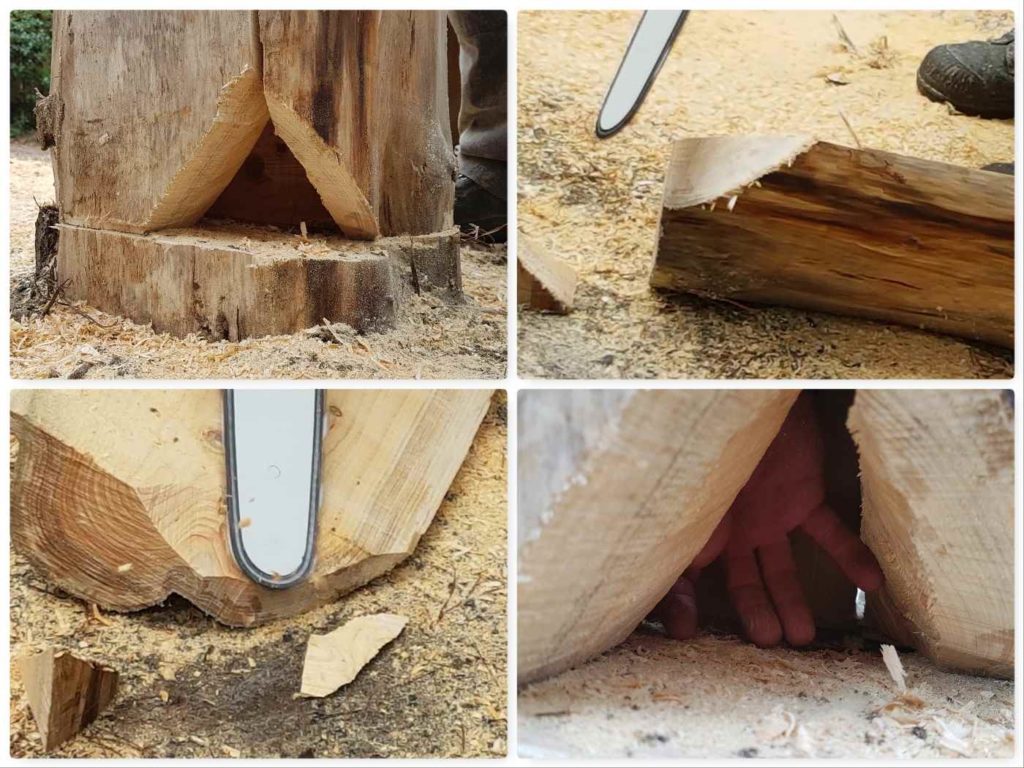
The Raappanan Tuli cuts
To increase the surface area of the chimney and help the log catch light more quickly I asked Rob to makes some cuts in the flue area. I got this idea from researching different types of log fires – this style of cut comes from the Raappanan Tuli log fire.
These cuts are particularly useful when you have a damp log as the increased surface area greatly increases the chances of the fire taking properly.
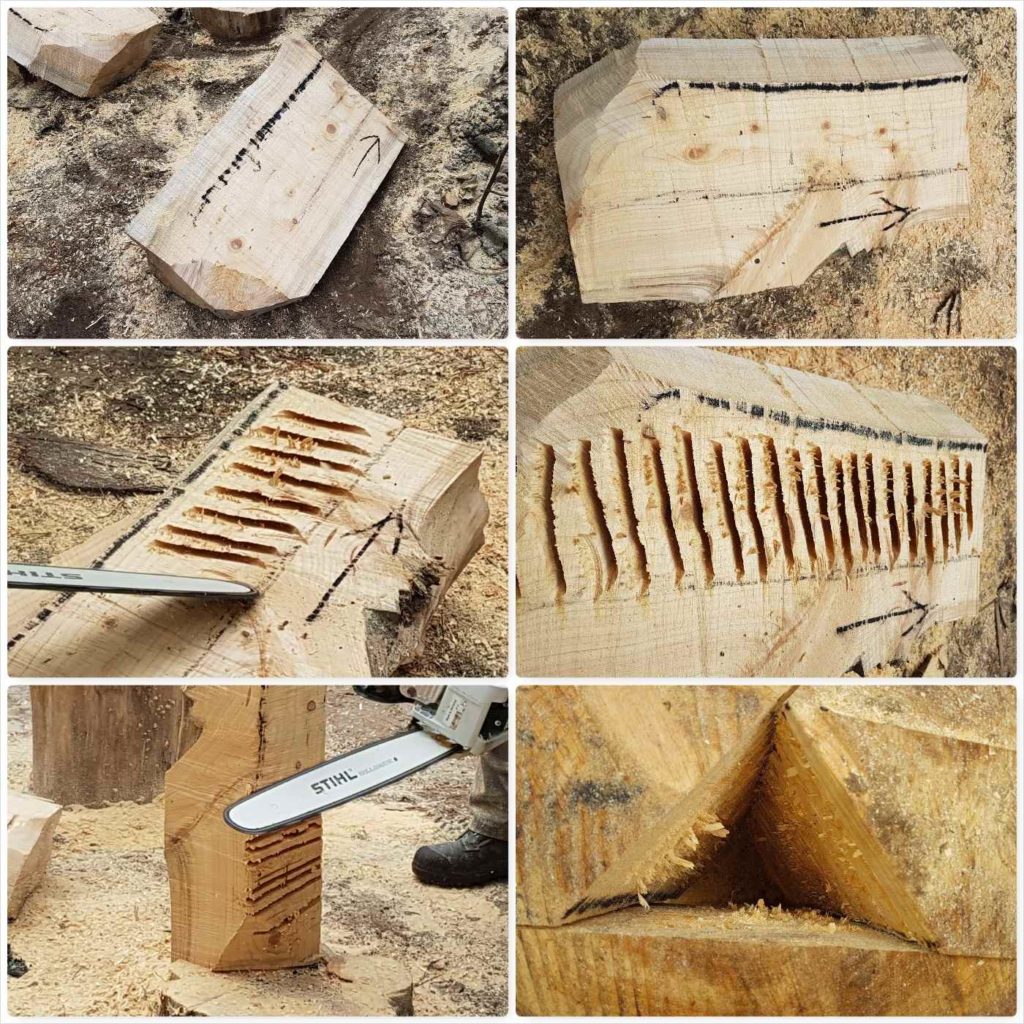
Final touches
I used strong wire to hold all the pieces of the reassembled log together – an alternative would have been to make some dovetail joints and join them together with green wood pegs – see here for more details – How To…. Build a Dovetail Log Rocket Stove.
Finally my friend Mark used his drill to give the log rocket a face (which also helped provide a bit more ventilation).
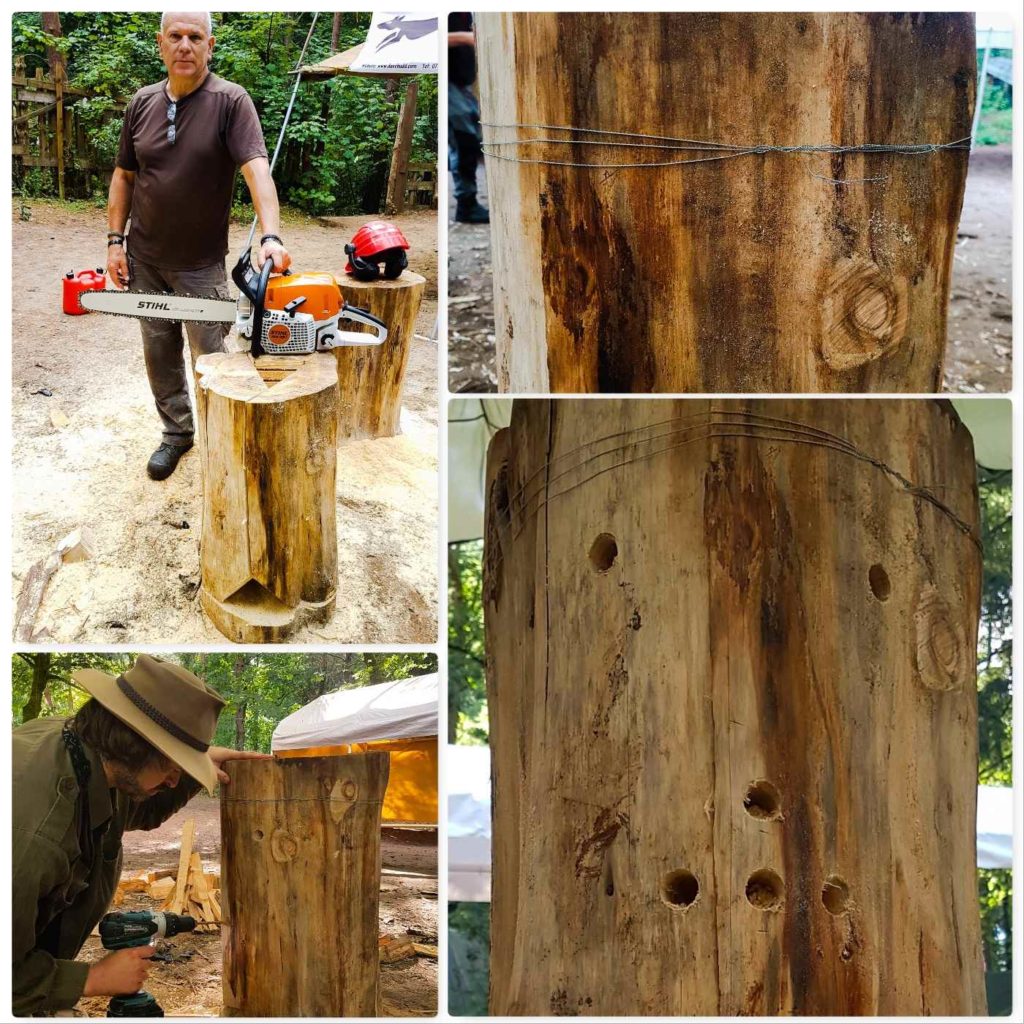
Firing up
I used slivers of the central section Rob had cut out of the log as kindling and lit it all with a lollistick lighter (a firelighter pierced on a sharp stick – have a look here – Lolli Stick Fire).
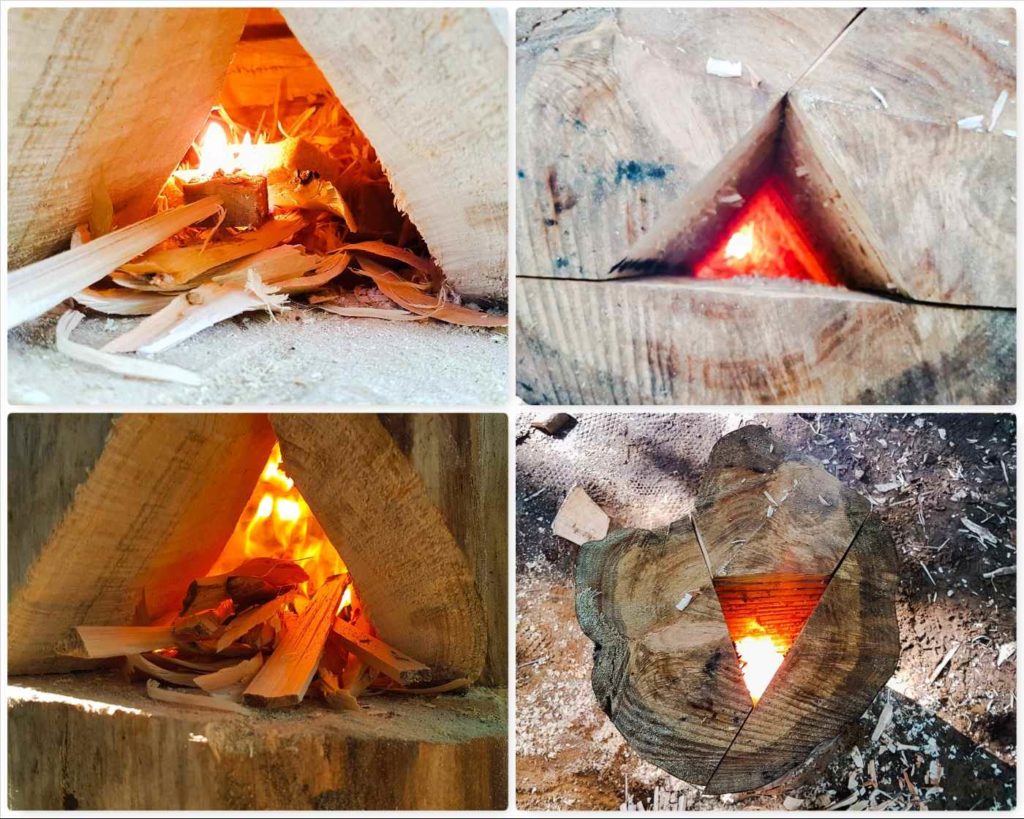
Party time
The log rocket was a stunning central feature for everyone to sit around in the evening and we even used it as a backdrop in a wedding photo (Magdalena and Phil renewed their vows at the Bushmoot).
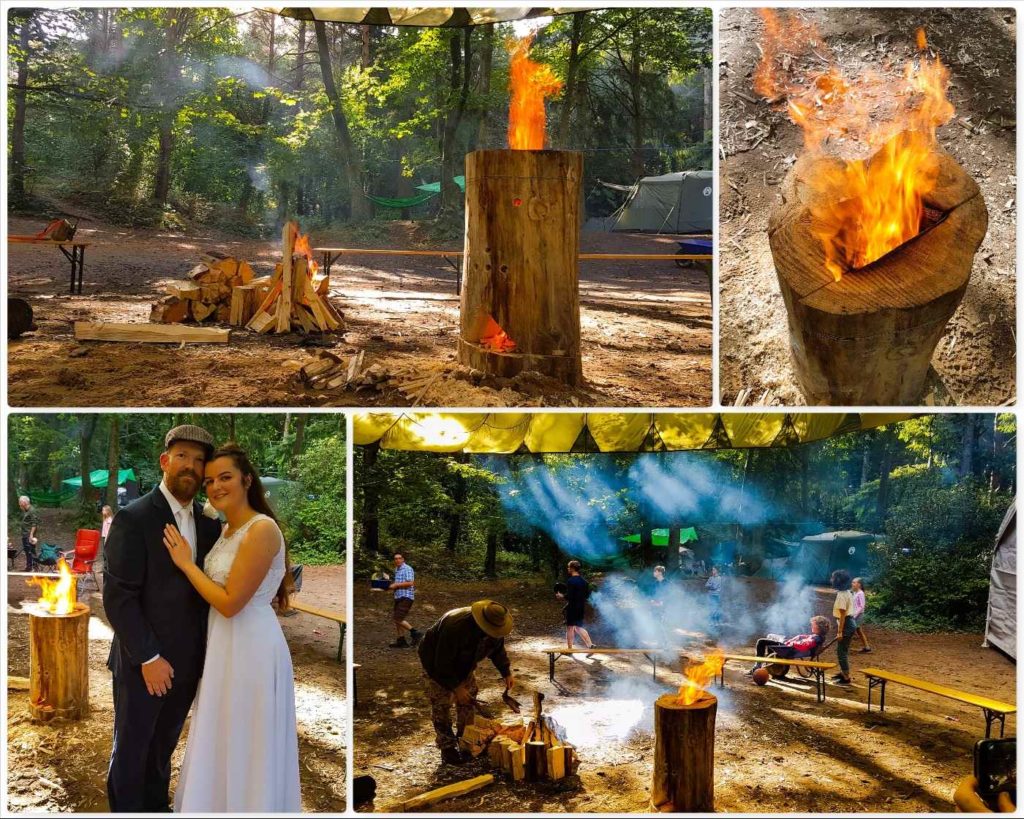
We even added a little bit of Cap’n Badger’s magic Rainbow dust to ‘mix the colours up’ a bit.
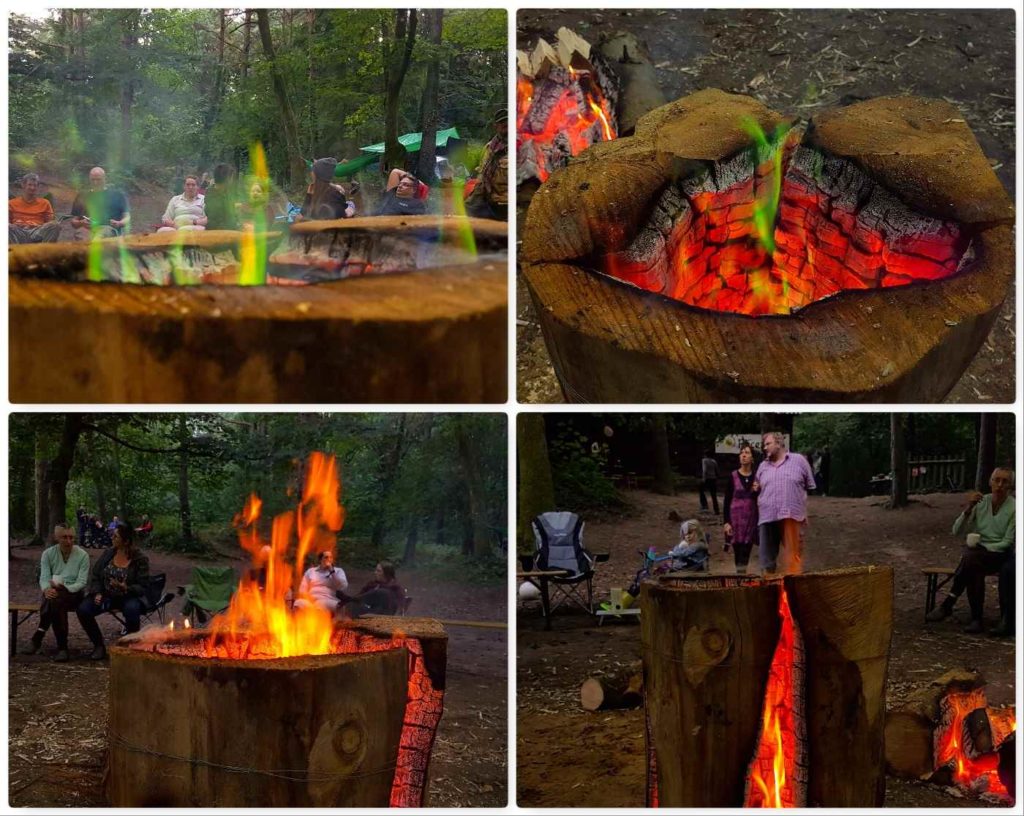
When I looked at the log rocket the next day (over 14 hours after it was lit) the base was just a mass of burning embers – quite a log rocket, I would say.
Cheers
George