The second bow I ever carved was a Holmegaard-style bow made out of ash. The bow on which I based my replica was found in a peat bog in the Holmegaard area of Denmark in the 1940s and is thought to be over 9000 years old. I made this bow while studying at John Rhyder’s Woodcraft School doing a Primitive Technology course. The wood that was available to us at the time for bowmaking was ash but the original bow found in Holmegaard was made of elm. The bow is a mixture of styles with the limbs that have a flatbow shape for half their length and ‘D’ sectioned like a longbow on the limb tips.
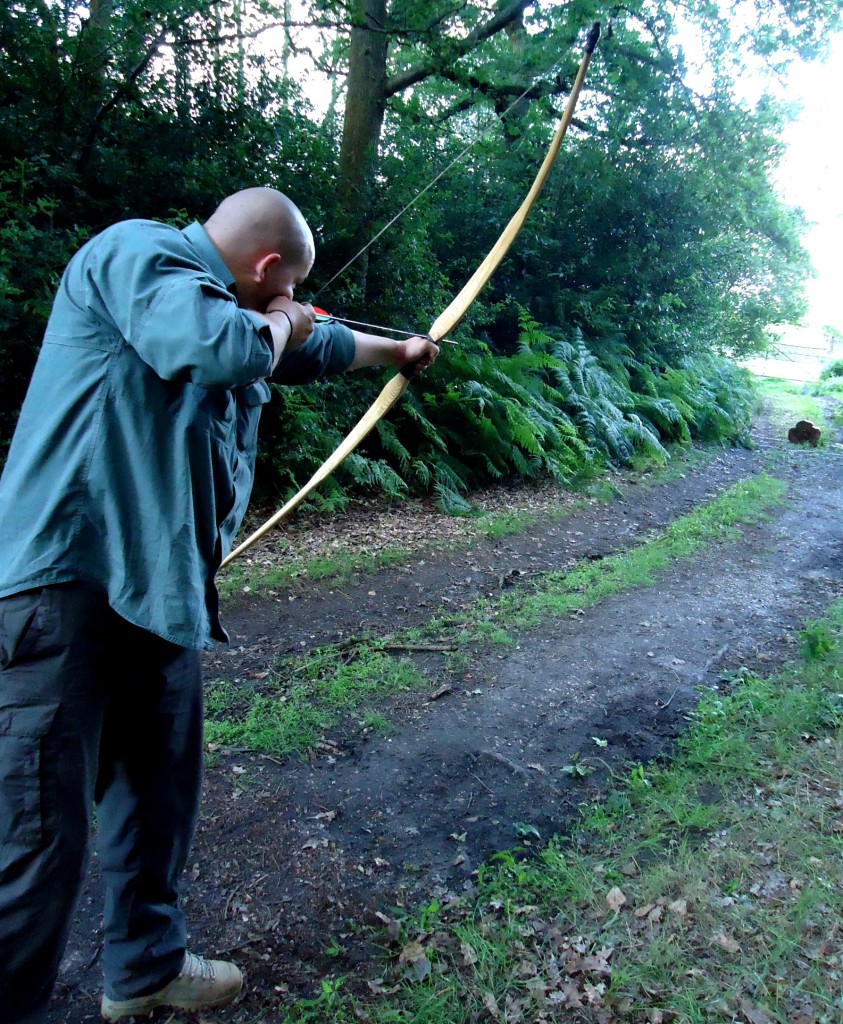
I really like this bow as it is very light in terms of draw weight but fast and whippy when it shoots owing to its ‘D’ sectioned tips. I have included in my previous post on Carving an Ash Flatbow explanations on different bow terminology and the differences between flatbows and longbows. Below are the rough dimensions I made my bow to – I tried to replicate the dimensions of the original bow as much as possible.
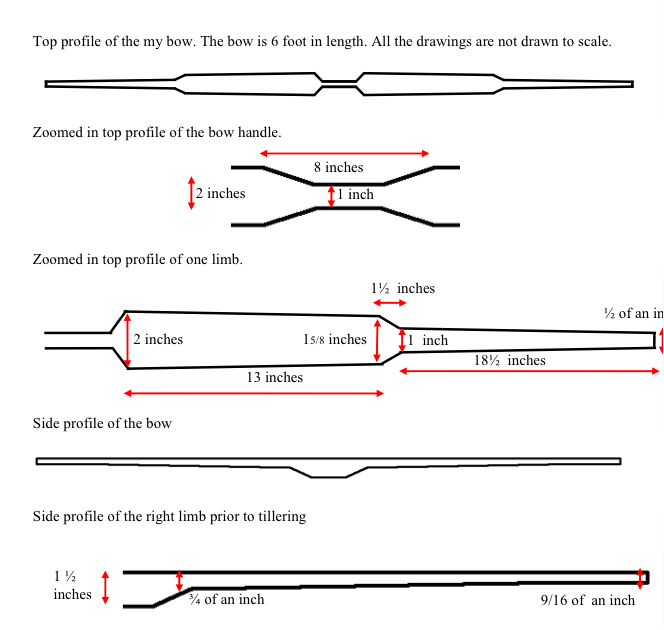
An ash tree had recently been felled and a section of the trunk cut down to just over 6 foot. I scored a line in the bark with a wedge down to the wood to help with guiding the split of the log. Note that the wedge is positioned to one side of the person scoring the line. This maintains a safe position for the worker. I then drove a wedge into the scored line to start the split at one end of the log (upper wedge in the top right picture). A second wedge was driven in at the base of the log to further split the log (lower wedge). Putting in the second wedge loosened the first wedge so I pulled it out and drove it in further down the line to widen the split.
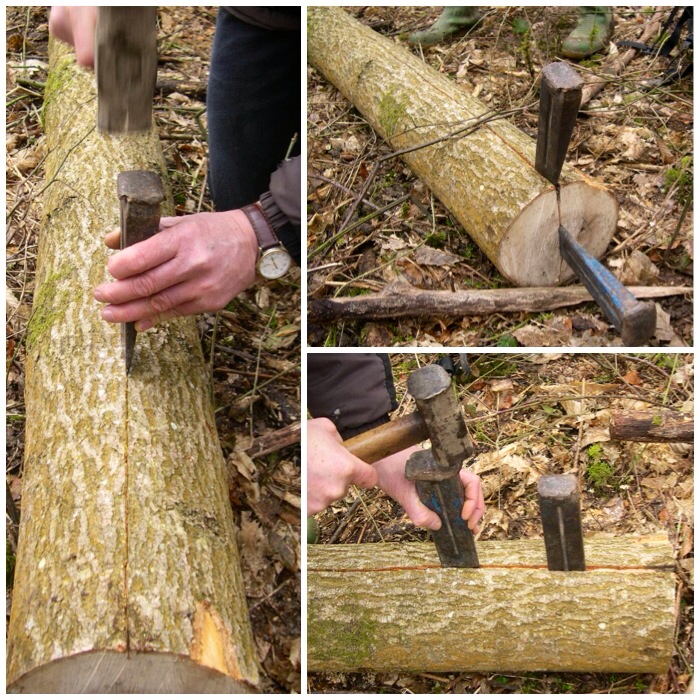
I just kept repeating this process of ‘leap frogging’ the wedges, and the scored line helped greatly with controlling the direction of the split.
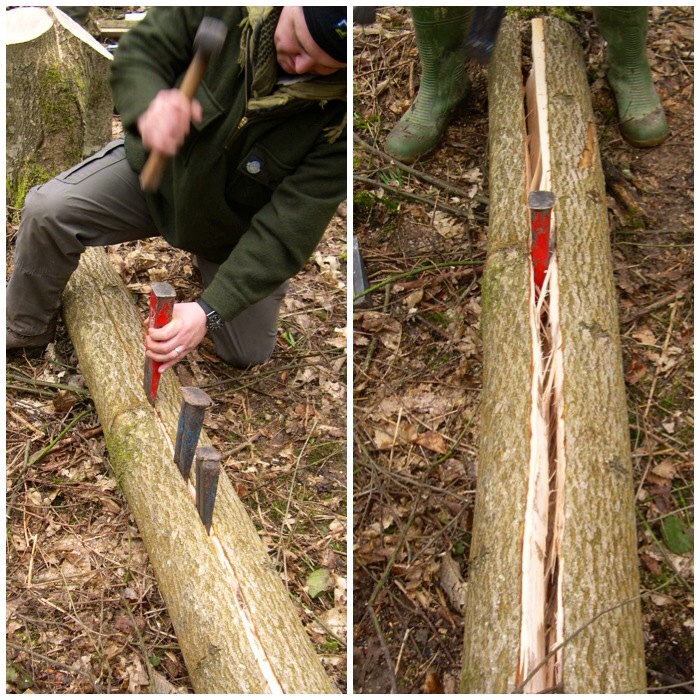
Once the log had been split I kept repeating the process again and again until all the staves were split out.
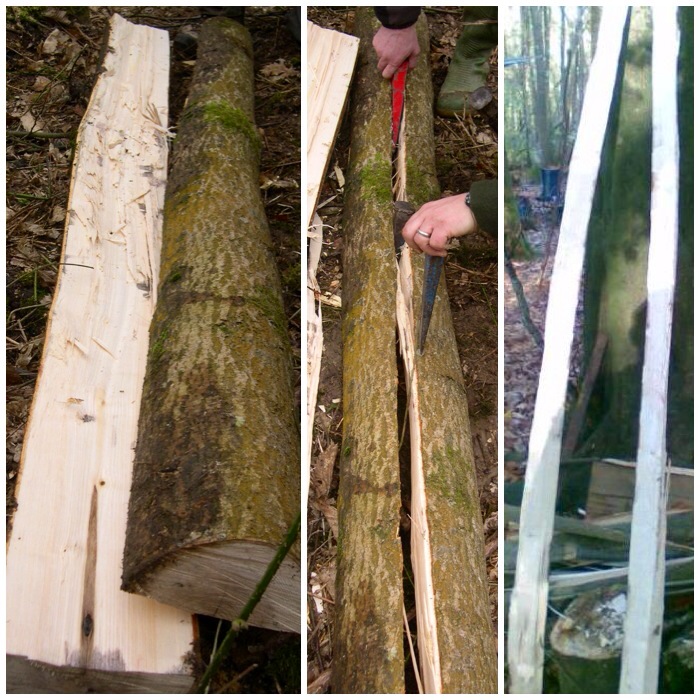
Using a wooden wedge I shaved off the bark of the stave. I was very careful to remove only the outer and inner bark and not to touch any of the wood. The wood found just under the bark is the most flexible part of the bow and will form the back of the bow. Apart from light sanding this area of the bow will not be touched.
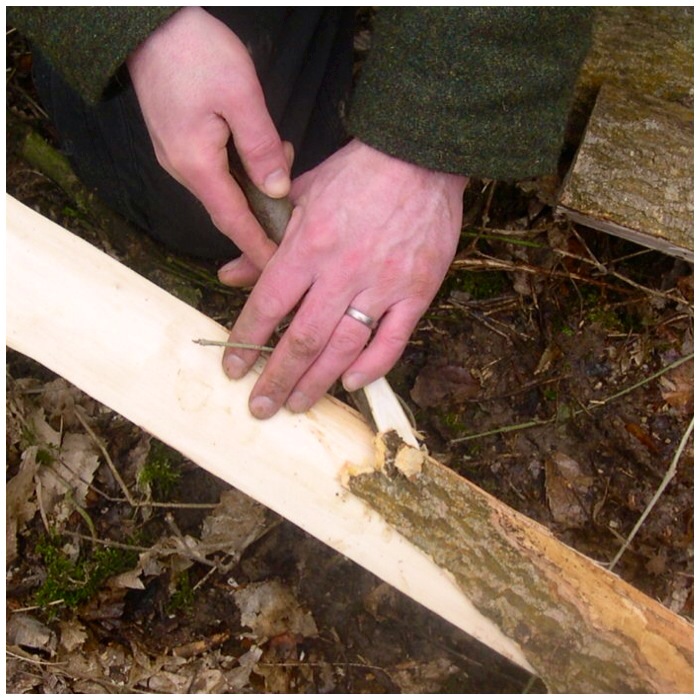
This is the side profile of the stave (top picture). The side profile has been roughly drawn out leaving plenty of room for error. A close up of the handle area can be seen in the bottom picture and the vertical lines are for the stop cuts.
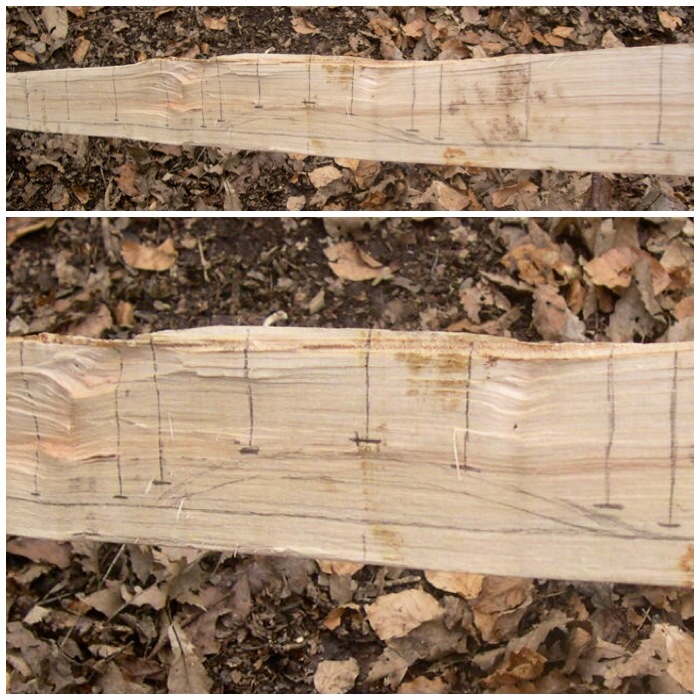
These stop cuts help greatly when getting rid of the excess wood. As the excess wood is cut out, the stop cuts prevent splits from travelling down the length of the bow. The top picture shows the area around the handle ready to be cut out and the bottom picture shows one of the limbs ready for work.
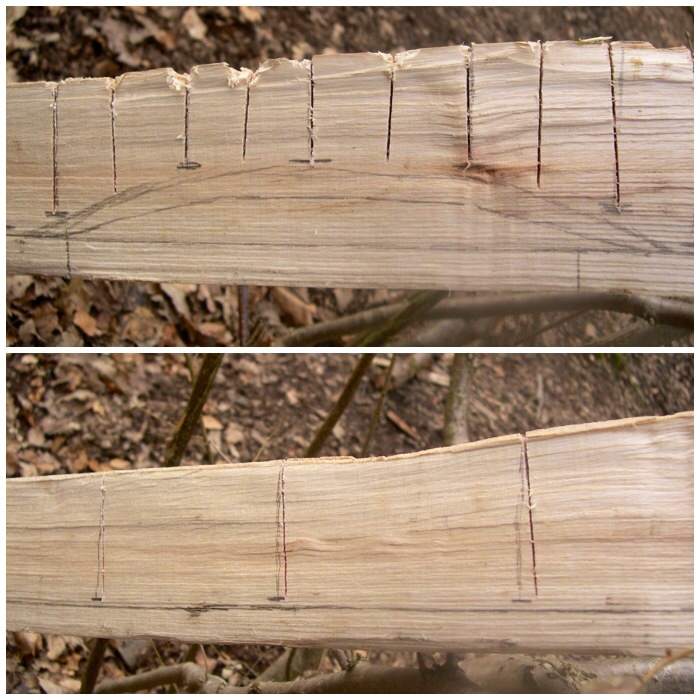
Some of the tools that are used to take off the excess wood: the axe for the start of the process and a knife and batton to finish it off.
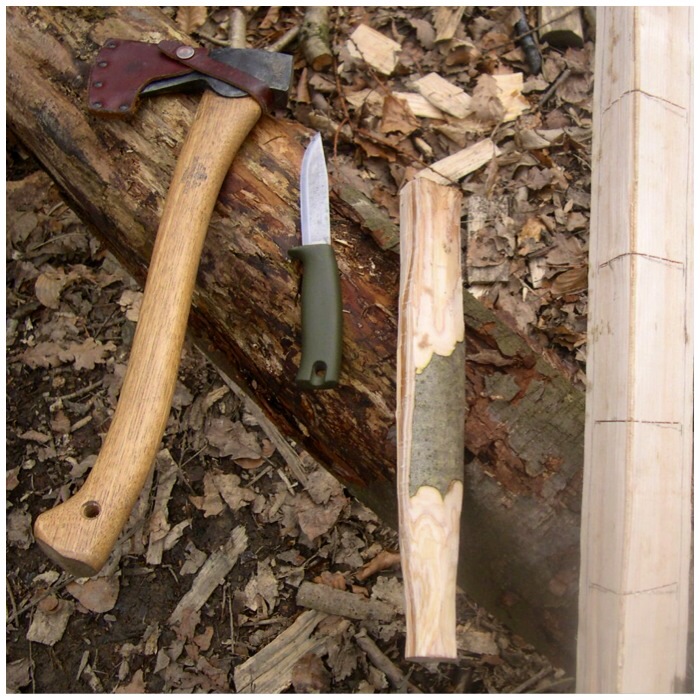
Keeping the stave off to one side of me and resting on a log, I trimmed the excess wood off. As the stave was off to one side I was in a safe position to work with the axe. If the axe had slipped its follow-through path would have been to my side.
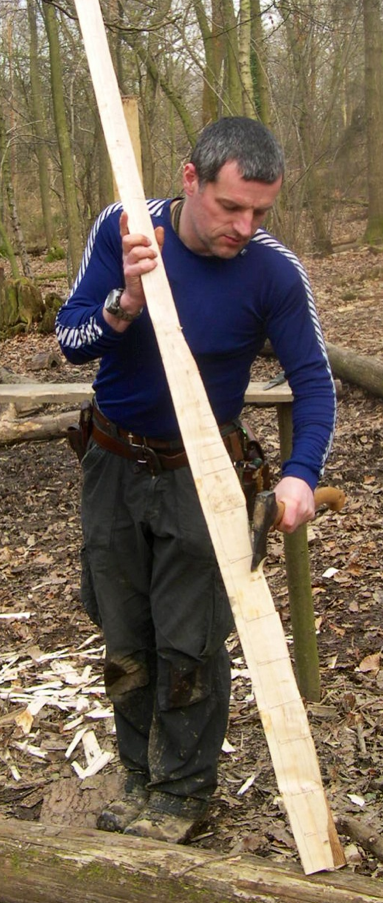
The tool on the left is a draw knife and can be used to finely trim the bow shape. If you do not have a draw knife you can embed the tip of a knife into a piece of wood to act as a second handle and use it as a draw knife. If you choose this method make sure that the piece of wood is on a secure flat surface before pushing the tip into it – never hold the piece of wood in your hand while you do this.
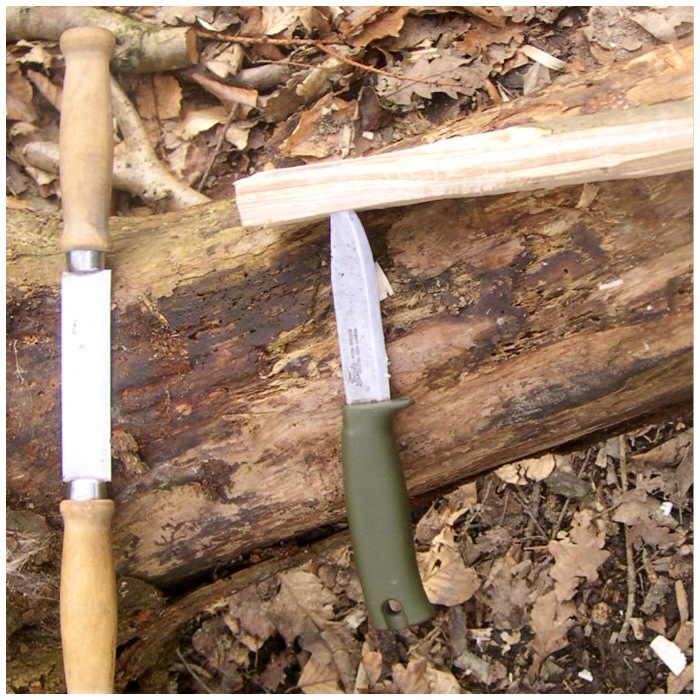
I clamped the bow securely to a workbench and then could easily start to use the draw knife. Here you can see the impromptu method in action; it works surprisingly well if your knife is sharp enough. It does not take long to work your way down to the line.
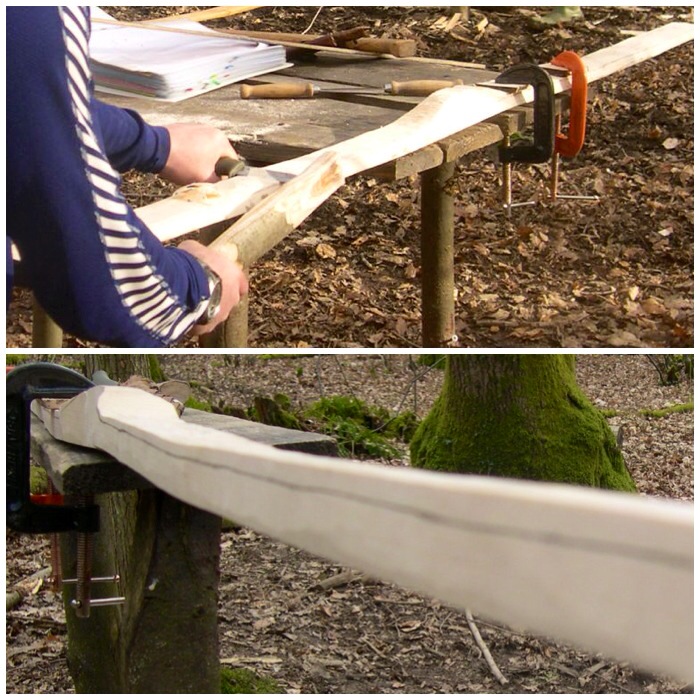
A lot of the time I braced the tip of the bow against my stomach as I removed the excess wood. As I worked towards the tip I repositioned the bow on the workbench so that it was held securely without needing to brace it. You can see the side profile of the bow emerging on the picture of the stave propped up against the tree on the right.
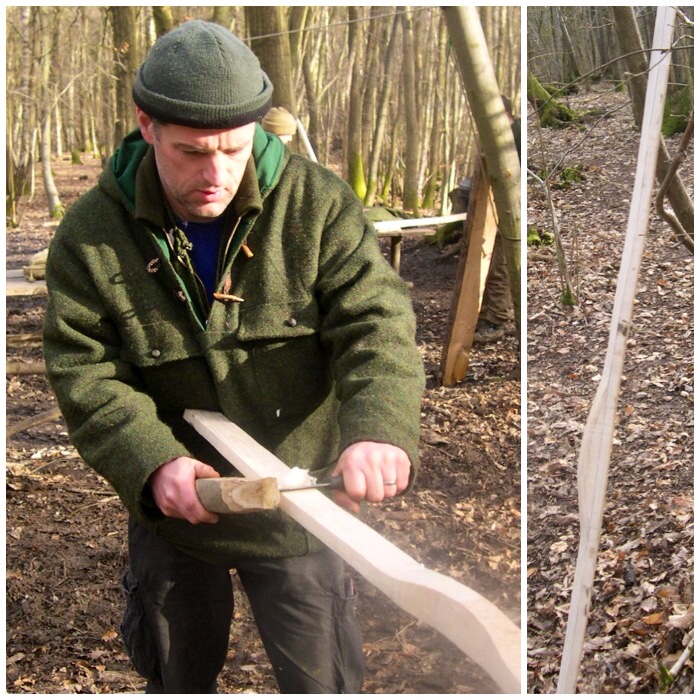
The next stage was to mark out the top profile of the bow. I used a string to mark out a centre line down the length of the stave (picture on left). Then using my measurements (shown at the beginning) I marked out the shape of the bow (picture on right).
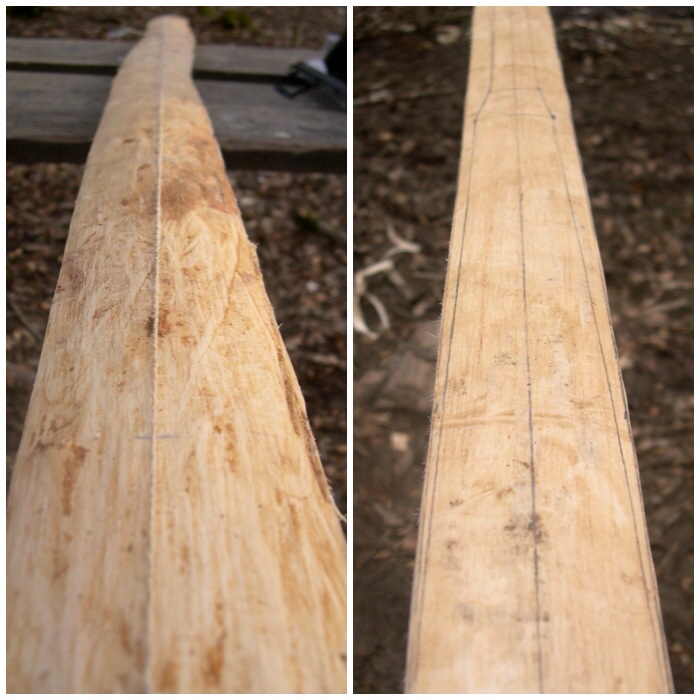
The picture on the left is the handle area I drew out and the one on the right is of one of the limbs. Both now have stop cuts sawn in to help with chopping out the bow shape.
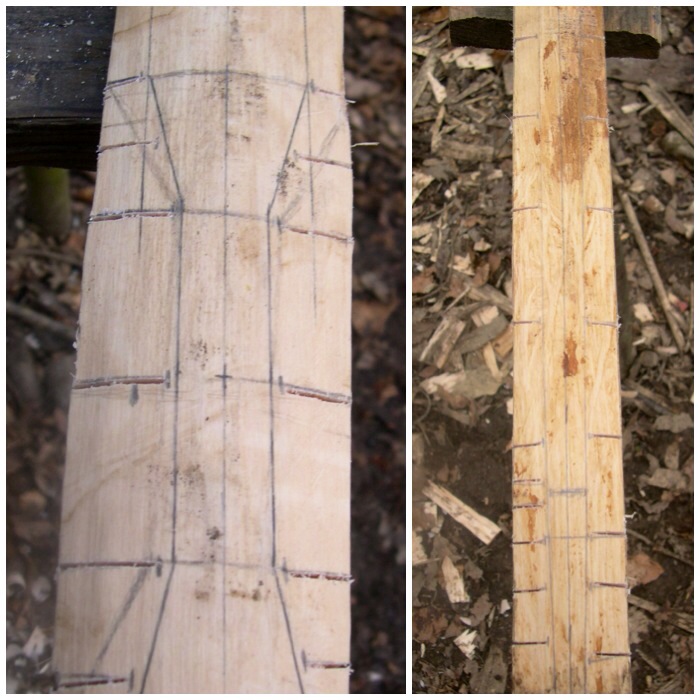
I enlarged some of the stop cuts to make sure that no split would travel very far. I find that jamming one end of the bow against a tree helps with the axing-out process and that it can be done in a much more controlled, safe manner so that the axe blade can never swing into me. It’s important too to use the axe in a safe and controlled manner. In the bottom picture you can start to see the handle shape appearing.
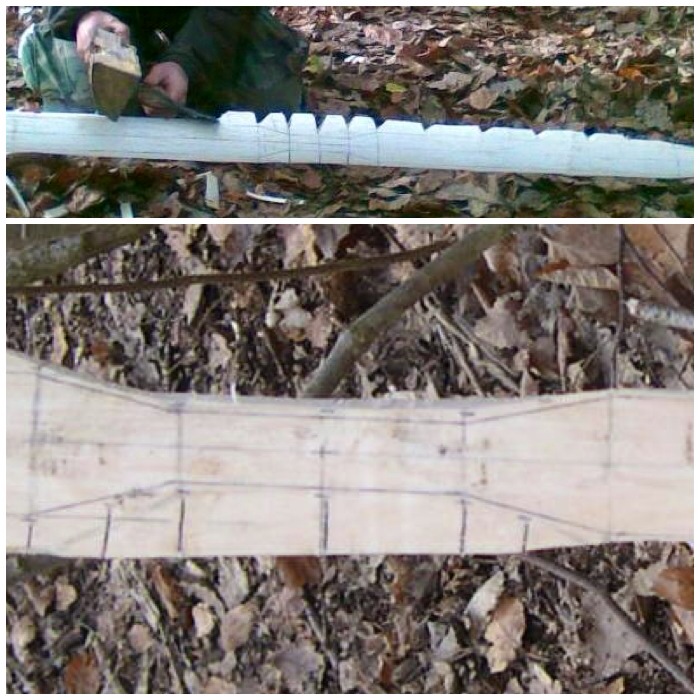
As well as taking off a lot of wood quickly, the draw knife method is useful for taking off fine shavings as you get down close to the line.
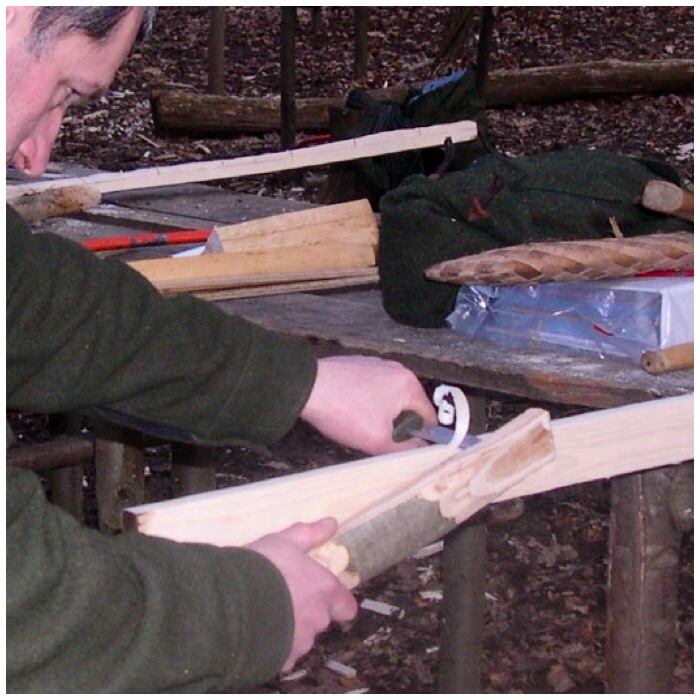
The top profile slowly started to appear as I finely carved the excess wood down to the line.

The draw knife was very easy to use as the angle of the limb changed from a Flatbow (near the handle) to a more ‘D’ shaped Longbow limb near the tips.
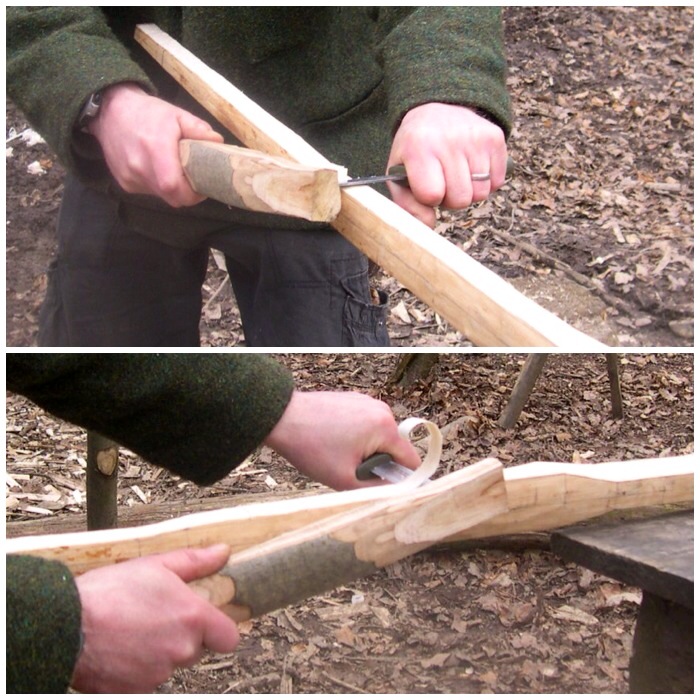
The ‘D’ sectioned shape of the tips soon started to appear. It was at this stage I decided to let the wood season for a month before doing any more work.
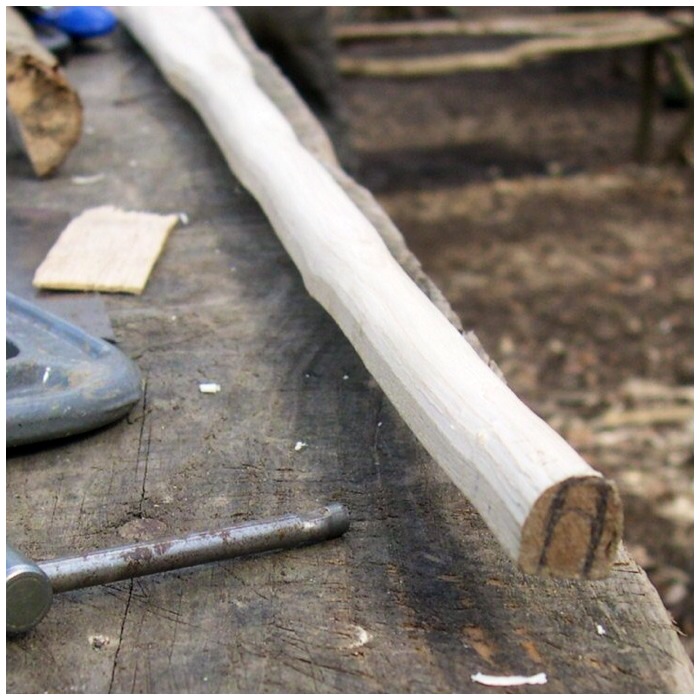
I seasoned the wood for one week in my garage and for three weeks in a cool spot in my house. This allowed the wood to season enough to start the fine work. During this seasoning process I tied the bow into a frame to induce some reflex into it.

One month later it was time to finish the bow. I started work on the tips of the bow so that they would have more of a ‘D’ section shape to them. Making the tips smaller meant there would be less weight in them, allowing them to move forward faster when shooting an arrow. Using my knife as a draw knife I was able to finely carve the shape of the ‘D’ section on each limb. As the tip of the knife is firmly embedded into a piece of wood it is very safe to use and highly manoeuverable.
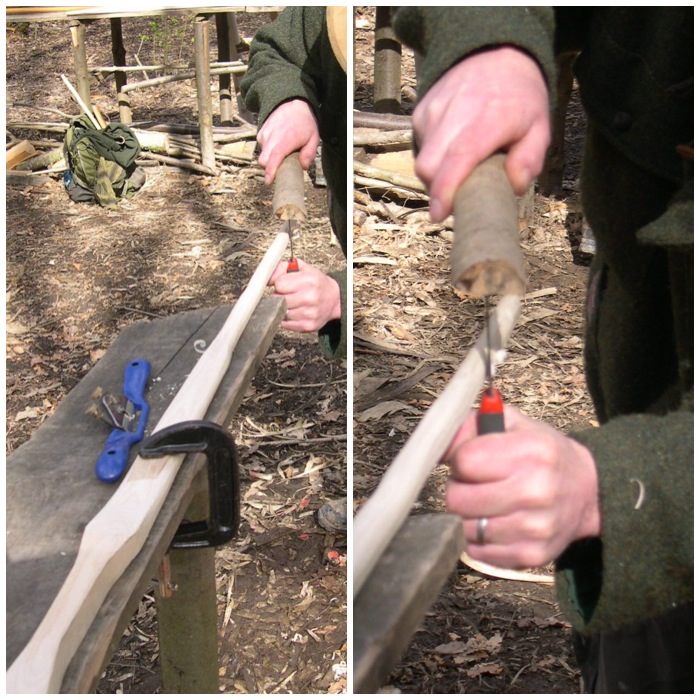
On each tip I came right down to the line but not past it with the draw knife.
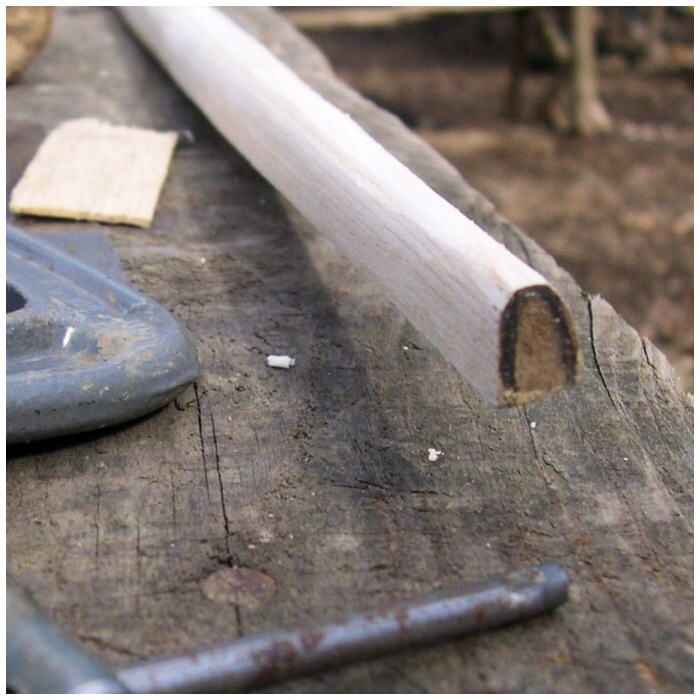
Up to this point I had tested the bow’s flexibility by floor-tillering it. This involves pushing down on the limb and checking to see if I was getting a nice curve or if there were areas of stiffness.
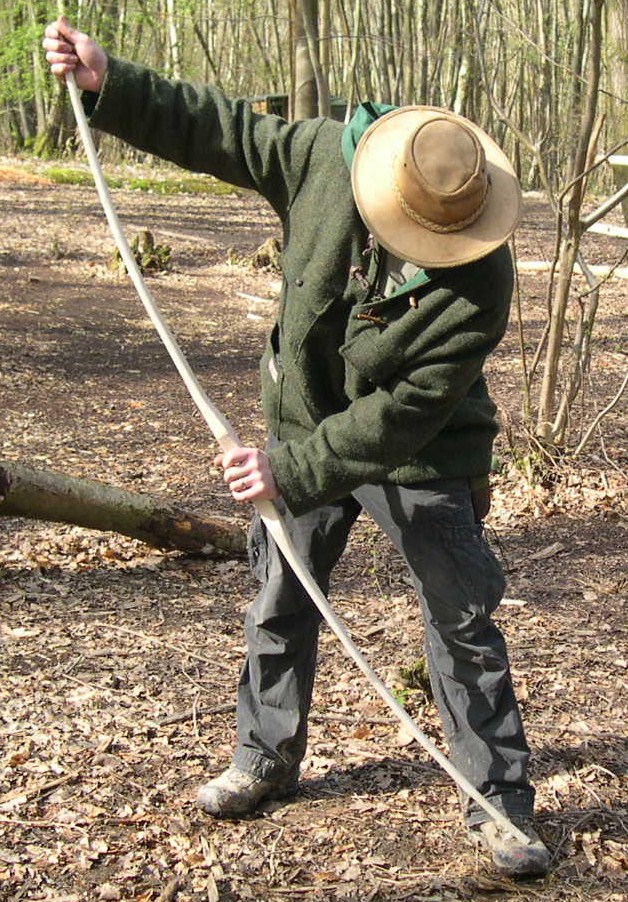
To take off excess wood from areas of stiffness I used a metal cabinet scraper. The scraper only takes off minute pieces of wood and is ideal for this part of the process. I carried on this process of scraping and floor tillering until I got a fairly good curve on both limbs.
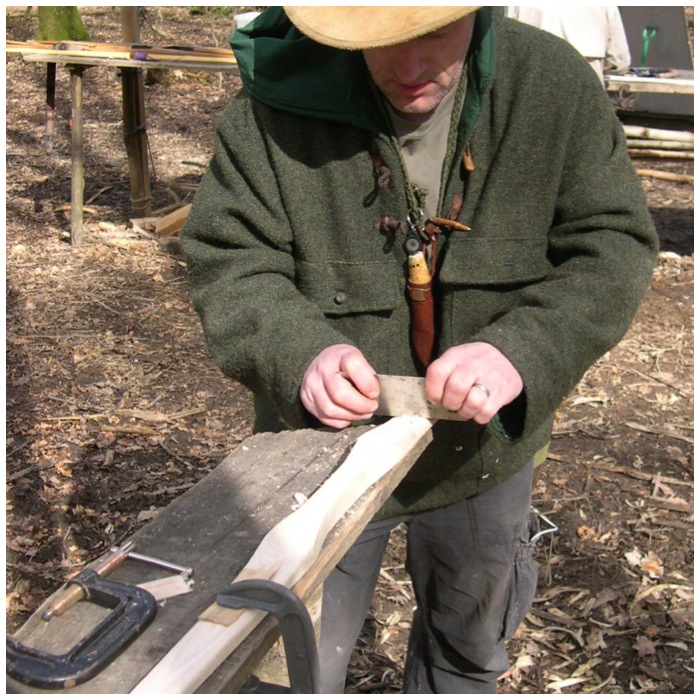
Before using the tillering pole to finely check the curvature, I had to add knocks to the bow. Some Holmegaard bows have been found without knocks carved into them and it is thought that they may have had bone-tipped knocks added, or some sort of wrap on each limb as a knock. I decided as an experiment to make a knock from some material wrapped around the tips of the limbs. I first tried cordage made from western red cedar bark, but I found that this did not grip the wood firmly enough and kept slipping.
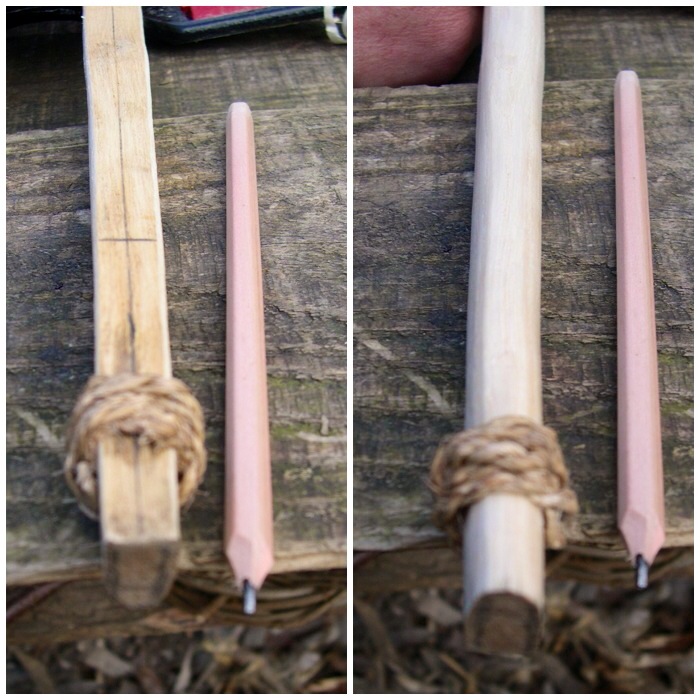
Next I tried rawhide, soaking it in hot water and then wrapping strips onto each end. This took about one and a half days to harden but allowed me to string the bow.
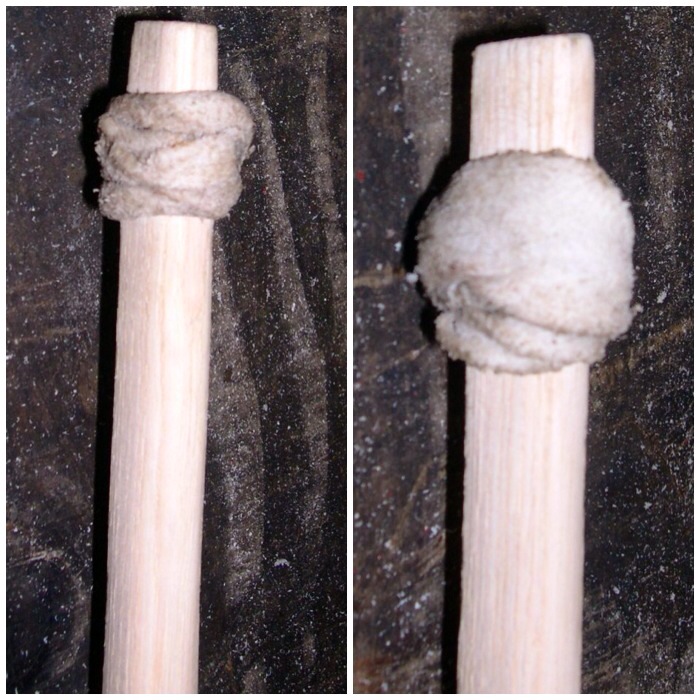
I coated the rawhide in pine pitch to waterproof it so it would not soften and slip if it got wet.
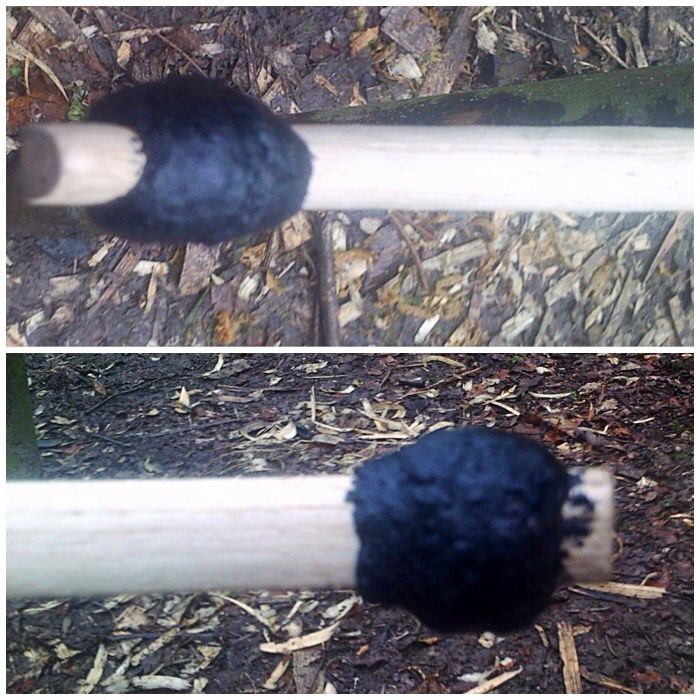
I just used some strong nylon string at first as a bowstring before starting the tillering process, tying on one end of the string with an overhand loop and the other end with a timber hitch. The string was just tied loosely, with no brace height. This picture is from when making my ash flatbow but the principle was exactly the same. Dick Baugh wrote a good article on tillering on the Primitive Ways website that is worth a read.
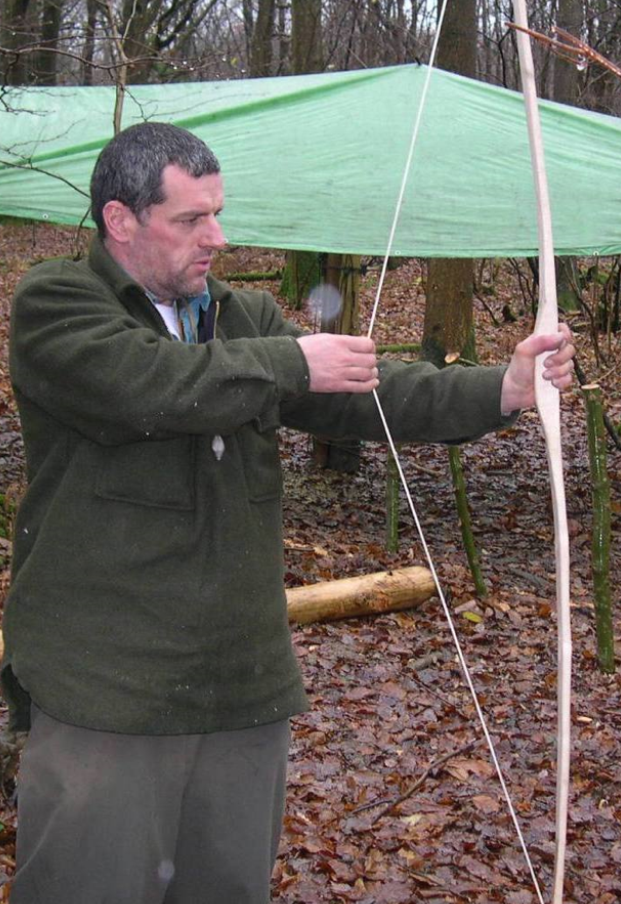
I then placed the bow on the tiller and in increments slowly bent it to view the curve on each limb. The pictures are of the bow during the tillering process. After viewing it each time I would return to the workbench to scrape wood from areas of stiffness using the cabinet scraper or spoke shave. Also I would raise the brace height a little by shortening the bow string to see how the bow reacted under pressure when braced. This whole process ensures you get a good even curve on each limb and also trains the bow to bend properly.
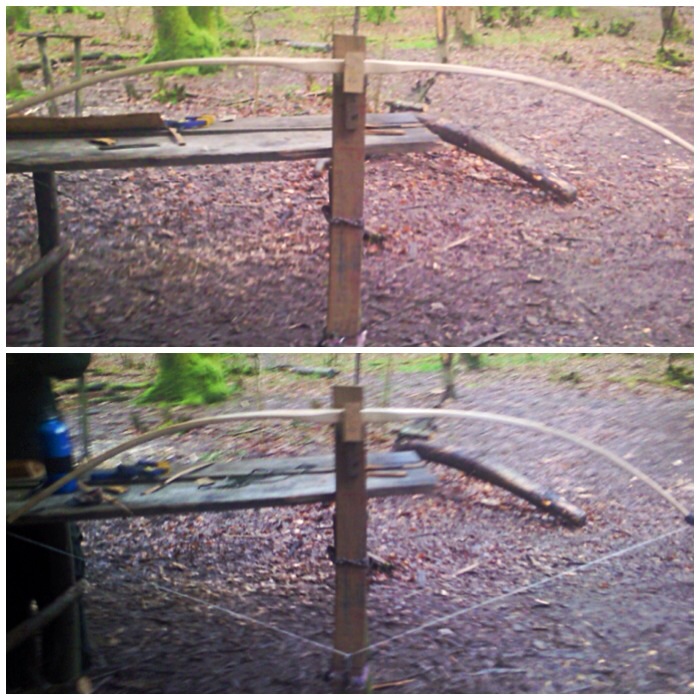
This picture was taken at the end of the tillering process with a 4 inch brace height: I was happy to take my first shot now.
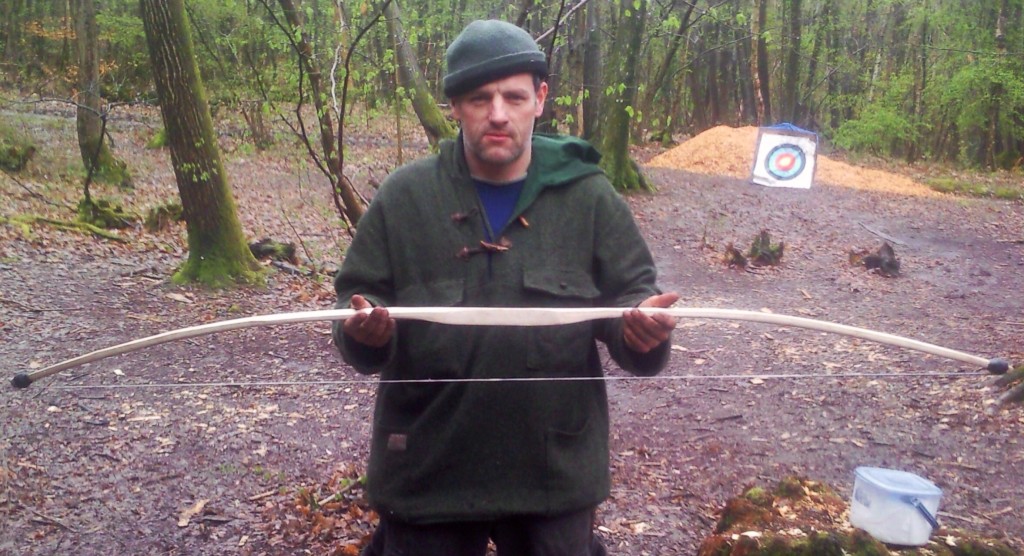
Having seen a few bows in my time still fail (split) at this point, I only drew back on the string about two thirds of my normal draw length for this first shot.
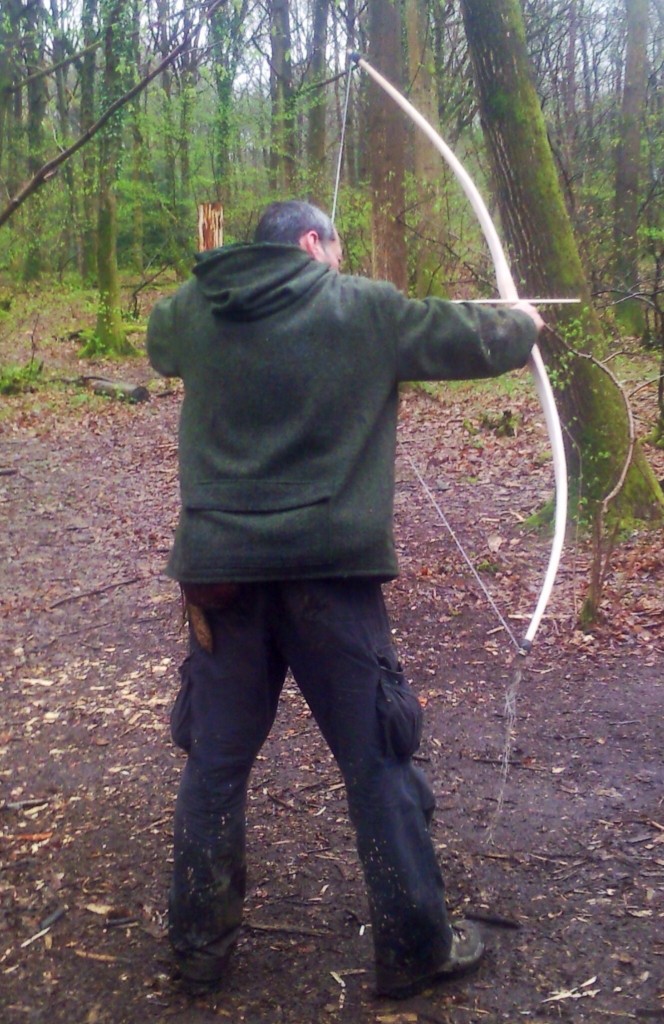
I then set about making my proper bowstring, which consisted of a Flemish twist on one end, a timber hitch on the other and serving the bowstring. Two good sites on this are Sam Harper’s site Poor Folk Bows for the string making and the Archery Talk forum for serving the string.
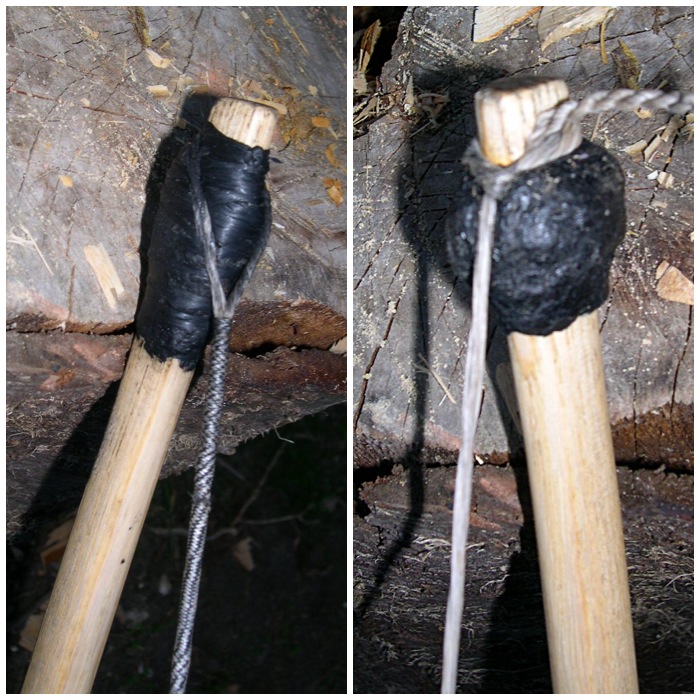
I used various grades of sandpaper to sand the bow down to get rid of any marks and sharp edges.
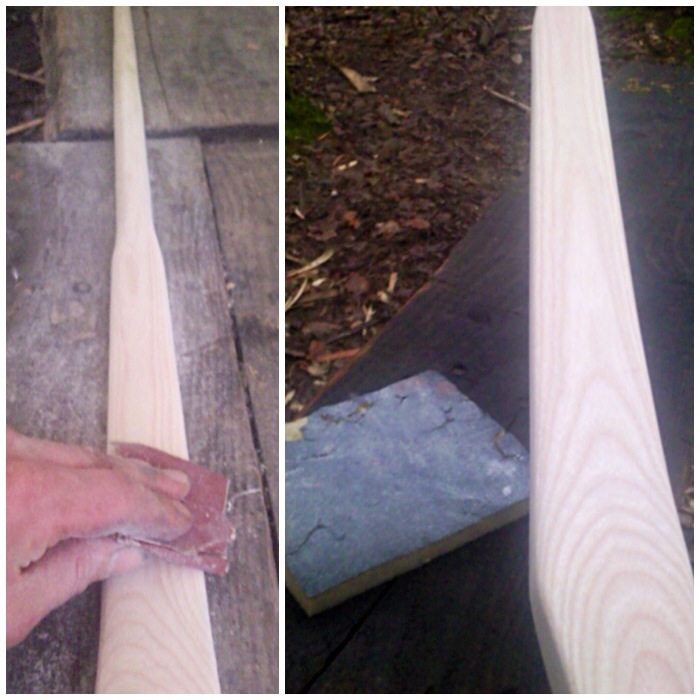
To protect the bow I stained the wood slightly. Then I applied a mixture of boiled linseed oil and white spirits (50/50 at first). After this had dried I reapplied more oil, but with less white spirits each time until by the end I was applying just oil.
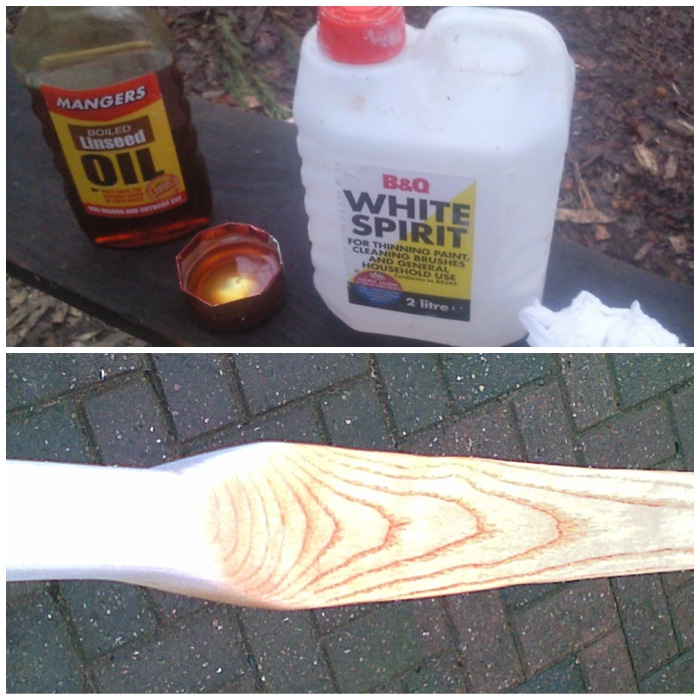
The next stage was to bone the wood by rubbing the whole bow with a small smooth pebble. This helps to close the fibres, making the bow very smooth, and also helps to lock in the oil. The whole process of boning can take a few hours but leaves a very smooth and shiny finish.
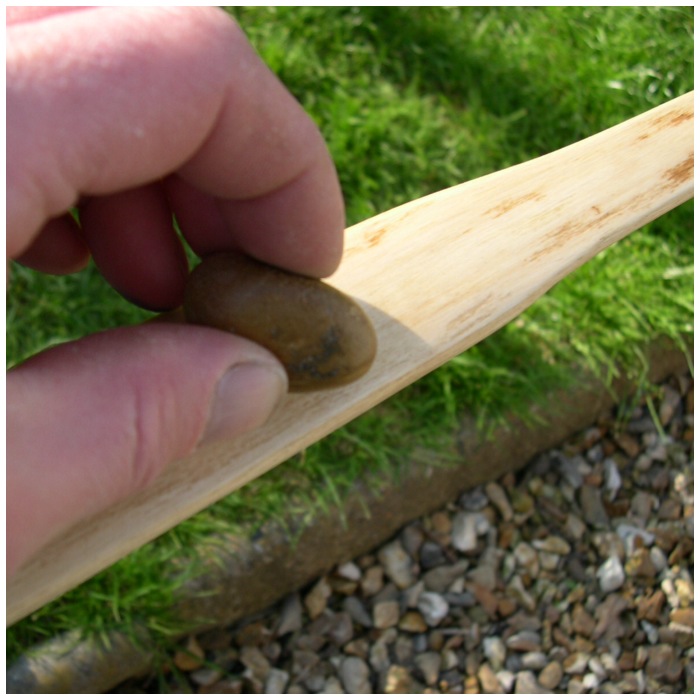
Lastly I wrapped on a small leather handle secured with a little glue. I thought about stitching one on but felt the seams might be too uncomfortable when holding it.
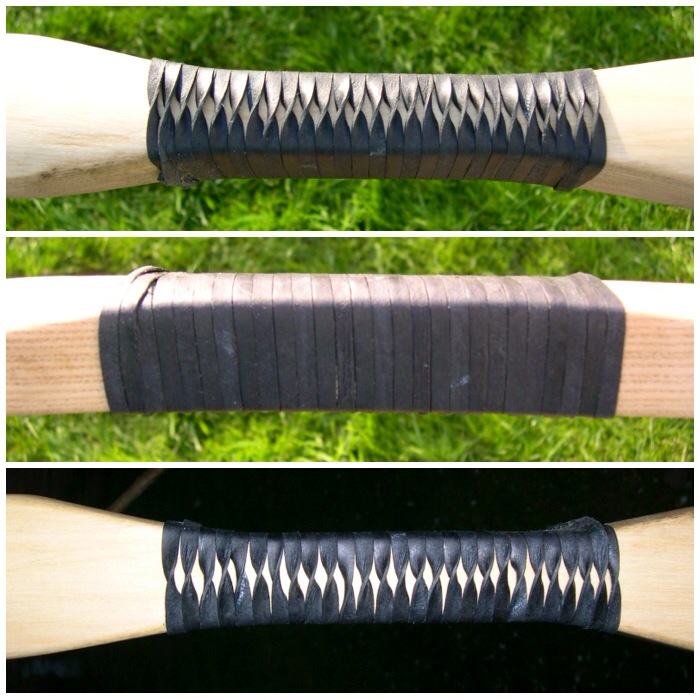
The completed bow showing the belly, side profile and the back..
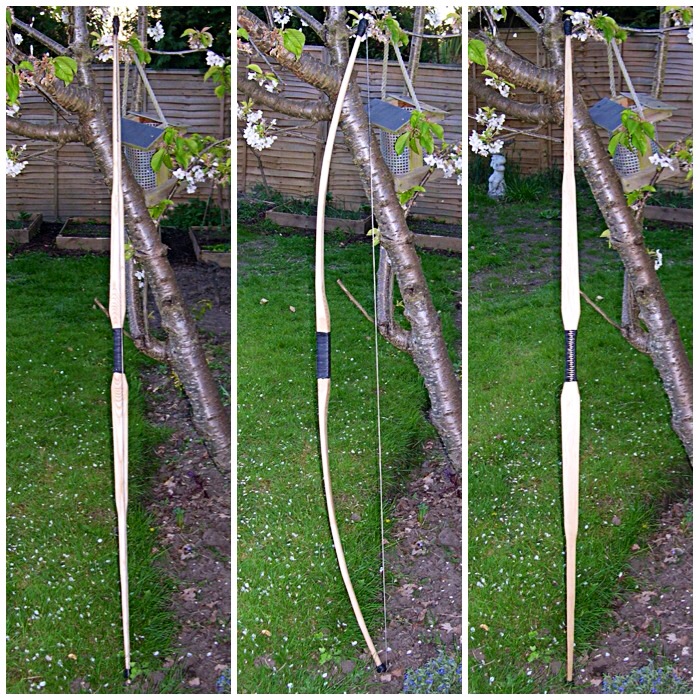
I am so glad that the rawhide knocks worked so well on this bow as they were something of an experiment. I don’t know if the size of the knocks slows the limbs down when shooting, but she does shoot fast.
This bow is particularly liked by youngsters as it is so easy to draw but still shoots fast. I managed to capture this arrow just after it had been released by the Holmegaard bow.
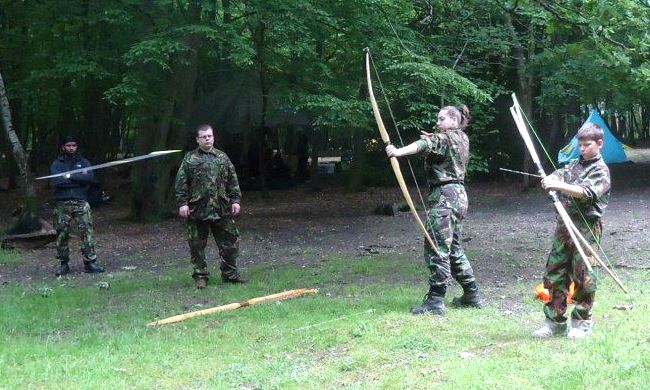
Cheers
George
Me like
🙂
great article thanks for sharing thinking of making my own oak holmegaard. and great pictures on the whole site love it! cheers
Cheers Dennis, Glad you liked it. I had a great time with John making this bow.
Cheers
George
Very jealous of that one George!
Cheers Tim.
It has been shooting well now for quite a few years and for about the last four Moots as well. Thanks for the share on FB as well.
Cheers
George
Very nice work mate.
Thanks st
George
I notice you have a fairly straight taper from inner fade to tip. How do you avoid having a hinge effect at the outer taper, where it goes from flat to D-shape? Am I also seeing a certain amount of flex in the rounded siyahs?
Hi David
The taper is very slight but enough to balance the the bow to stop a hinge. At the point of the taper on the D section the bow is wider than it is deep but at the tip the taper has worked on all planes so that the bow limb is deeper than it is wide.
This caused me a lot of problems with the sinew knocks as they just kept slipping until I managed to wrap them tight enough.
As to the siyahs I agree that there is a certain amount of flex just up to the point of the sinew wrap. The D section helps I think in overcoming this potential loss of power by its D shape. These parts of the limbs really whip forward as they are very aerodynamic and make the arrows shoot quite fast for such a light bow (in terms of poundage). I think that is why the bow was used in hunting but that is my guess only.
I made this bow (in particular the sinew knocks) as an experiment with John Rhyder of Woodcraft School as a number of Holmegaards have been found without noticeable knocks (horn could have been used but we decided on this approach to see if the theory would work). John is an excellent bowyer and would give you a far more technical reply than I ever could.
The bow is still shooting well over these last 5 years and is my favourite.
Cheers
George
Thank you, George, for the reply, I’ve only been making bows for a couple of years, after 45 years as a furniture designer/ builder, and find things oddly challenging, trying to carve wood so that it will bend nicely, rather than making wood that won’t move or warp. Your bow is one of the more handsome of this style I’ve seen, and I look forward to building one soon. I may try it in a bamboo backed ipe board bow since my staves are still curing, and won’t be ready for several months.
As for the sinew nocks, although it would be a serious diversion from the traditional-ity of the bow, I’ve had some experience with a product known as “liquid insulation”, available at any electric supply, which is a black, gel type of application, which is not only a glue, but shrinks as it dries, which might make a very secure sinew nock.
hey George nice bow do you have a arrow rest or do you rest the arrow on your hand when you shoot it i didn’t see one.
thanks
Scott
Hi Scott
Thanks for posting.
I just use the forefinger on my right hand (I am left handed).
Occasionally when the flights are either plastic or badly attached this causes cuts on the knuckle area of the finger.
Cheers
George
check the position of your nocking point to avoid this. it should be about the width of an arrow nock above square
I love that improvised draw knife idea. That ranks with the improvised treadle lathe using a sapling, Coracle making, and the willow carved wife muzzle, with or without Oak Shoosh needles ;).
Ditto: Great improvised drawknife, as in Portugal spokeshaves and drawknives are like hen’s teeth! And the rawhide and pitch nocks are excellent, I am always wary of cutting the nocks and weakening the tips…this solves the problem.
Glad you liked the idea Nick. Good luck with the nocks. Get that rawhide as tight as you can 🙂
Thanks for the very detailed step-by-step and photographs. That really helps me understand. Your creation is very inspiring!
Love the how-to guide. What kind of green wool jacket is that you have on in the pictures?
Hi Merle. Glad you liked it. The jacket is made from Harris Tweed. I had it made by my wife. Cheers, George
great work. have you weighed it at all and or tested it for distance?. You know actual sinew shrinks a bit as it dries so should give a tougher nock than rawhide. Even very small grooves on the belly for it to grip into would help too. I’m putting little horn plates on one of my bows at the mo. glued with rawhide and bound with thin hemp fibres .
Hi Davey
Glad you liked it. It is a very light bow at just over 30lb in draw. The D section tips though really help it. On a high arc the bow can put an arrow 100m down range. It is though I think a close up hunting bow, light and snappy.
George, This is one of my favorite bows to make. I love the design, with the tapered limbs, which give it a nice, streamlined look, over my first Mollegabet bow, which maintained the 2″ width through the working sections, then went down to 7/8″ at the levers. I am working on a short , 59″ version now, with rawhide backing that might finish out to be around 50# @ 28″; if I get 45#, I’ll be more than happy! Thanks again!
Best of luck David. I have a Yew and an Elm stave waiting some attention.
I’m wondering if a fallen elm that is 3.5” in diameter is thick enough to make a bow from? I can send a photo if you provide me an email address. Thanks for all the amazing info.
Hi Kevin
A few of my friends have made bows out of limbs (using Hazel) that kind of diameter in the past. The back of the bow will be quite rounded but they work perfectly well. Give it a go.
Cheers
George