The main benefit is – is that the tea gets made
I was trimming an ash tree in my garden recently with my friend Paul and I managed to save a few pieces for Atlatls and pot hangers.
I have previously shown you how to carve a collapsible pot hanger so that it can fit into a pot when not in use but on a lot of occasions I just whittle one when I need one.
The type of pot hanger I am talking about is shown below hanging off a ‘Wagon/Waugan Stick’ (pronounced waygone or worgan – I hear different variations on this from different people) campfire set up. The pot hook is adjustable in that the pot is easily raised or lowered by using the different hooks on the pot hanger.
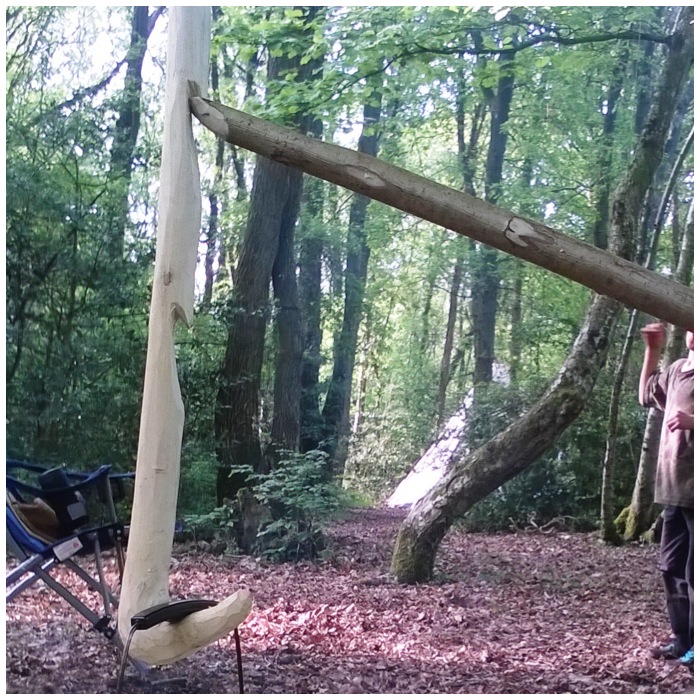
I started off with a piece of ash that had a fork in it at a good angle (to form a hook) and finished up with something that allowed me to be able to quickly or slowly cook/boil something.
On the right you can see the finished pot hanger in action. To help stop any confusion I will refer to the large hook holding the small kettle as the ‘pot hook’ and the small hooks as the ‘adjusting hooks’.
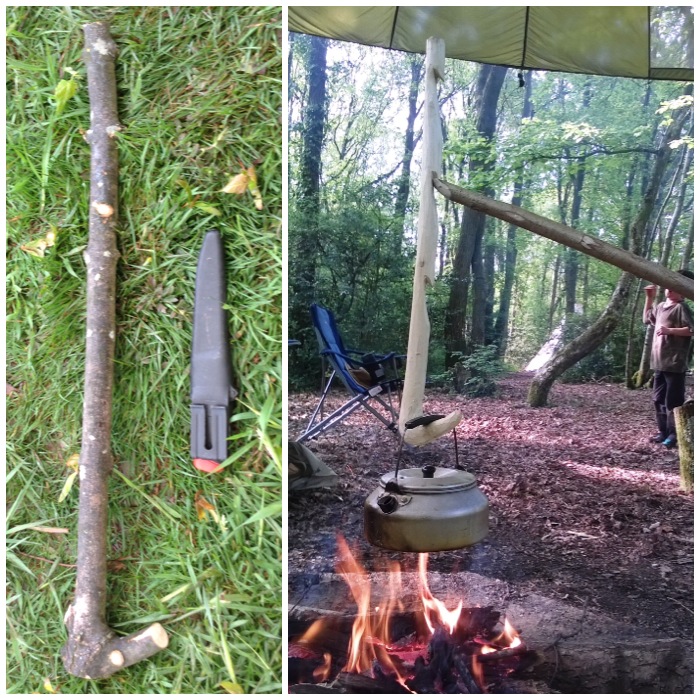
To begin with I trimmed off all the knobbly pieces using powerful chest lever and locked arm cuts. See my How To…. on knife Safety for more information on these types of cuts.
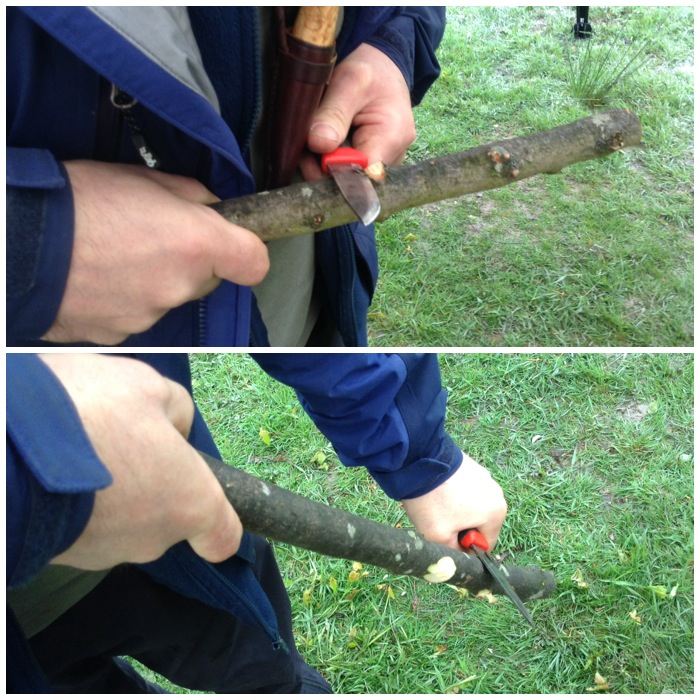
I then trimmed the bark off using a powerful shoulder cut. I had the work piece placed on the ground here off to one side so as to brace it and to work safely.
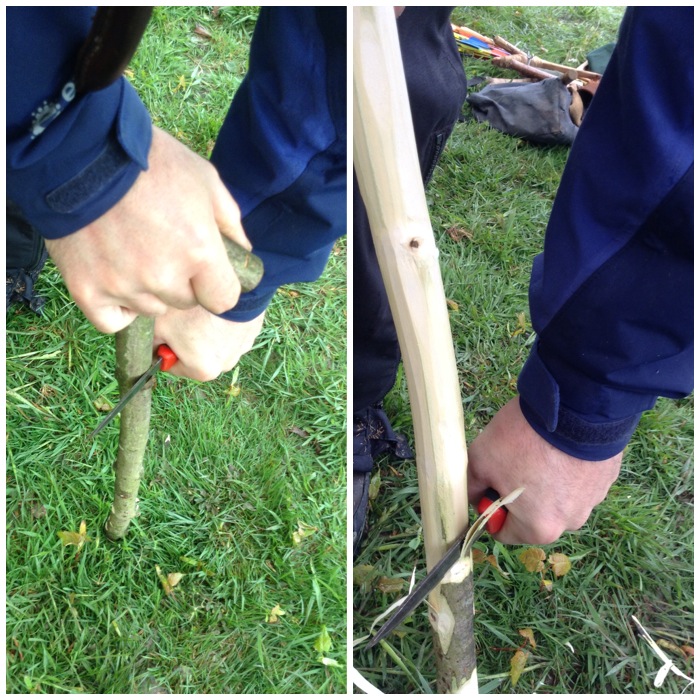
To strip the bark around the hook area I used a gentle chest lever grip.
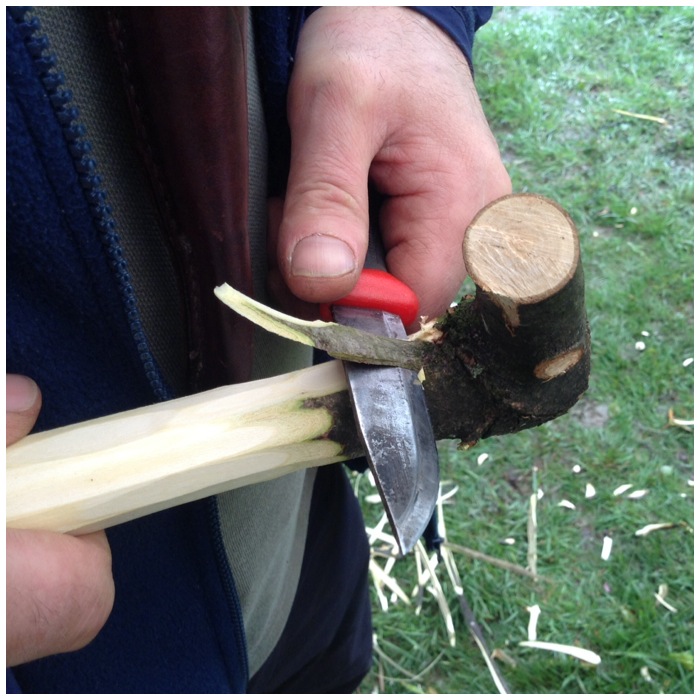
The bottom of the pot hanger was more difficult to trim as I had not left any excess wood to hold on to. The main thing I needed to consider here was keeping my eye on where my thumb was on the hand holding the pot hanger.
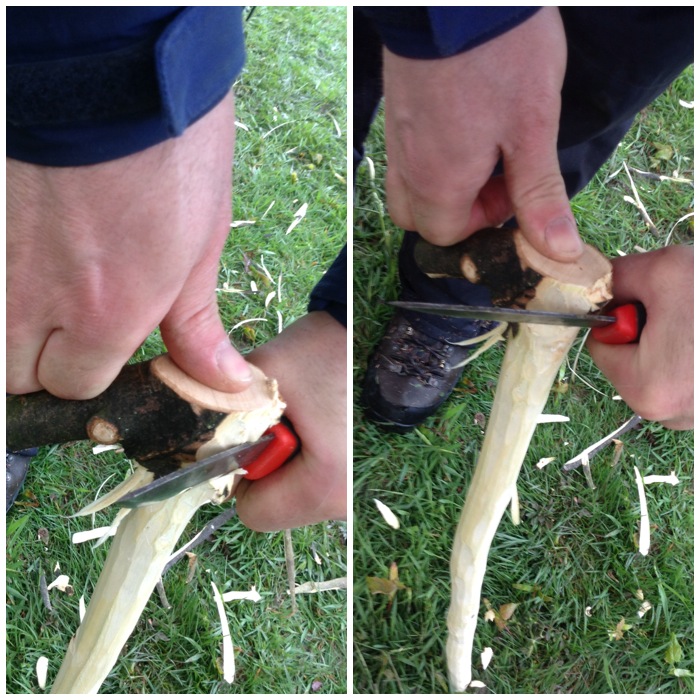
As I needed to use the point area of the blade to trim around the hook I kept the pot hook resting on a small log so that if the knife slipped it would hit the ground. My friend Charlie showed me how to use the knife and the curve of the pot hook to create a fulcrum, making the stripping of the bark safer. I tried to photograph this but they did not turn out well.
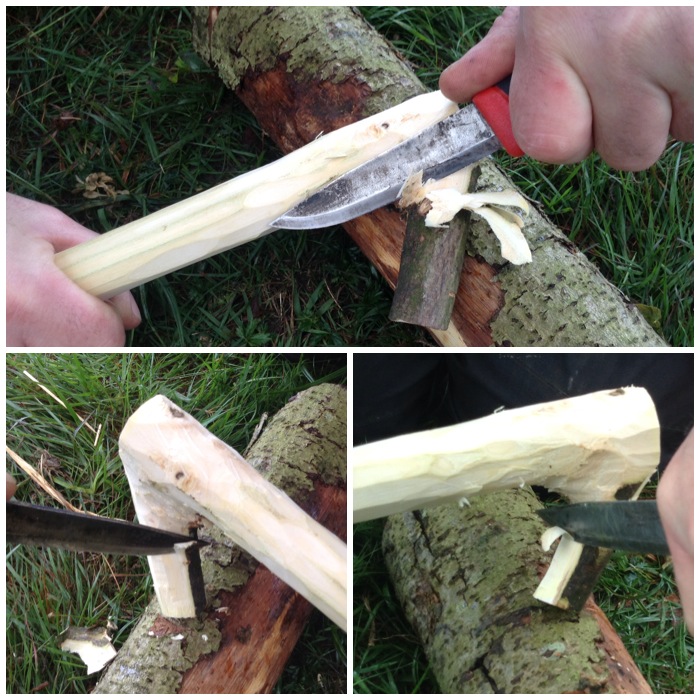
I also rounded the bottom of the pot hanger and then used the back of my knife to strip off the remnants of the inner bark.
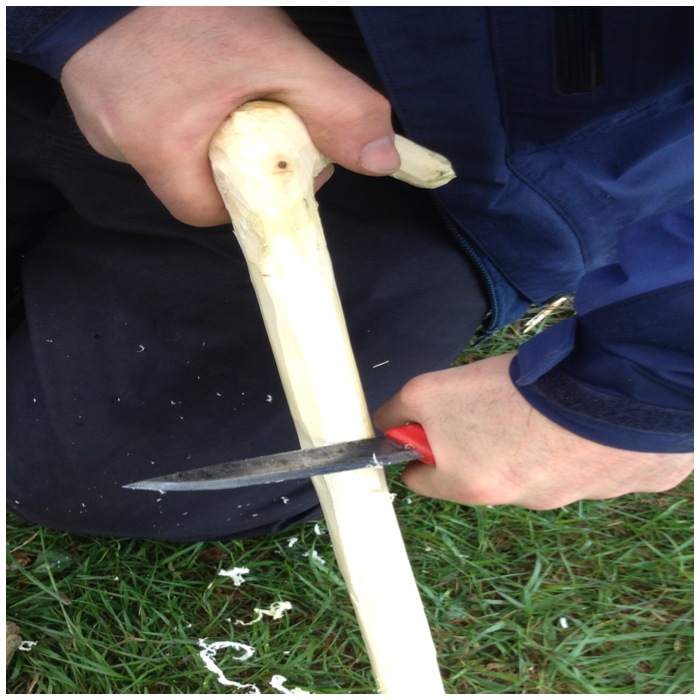
To make the adjusting hooks I used a batton (a large stick) to carve a cross into the wood – an X cut. I placed my X cuts in line with the pot hook as much as possible. After a couple of good smacks with the batton the knife had cut well into the wood.
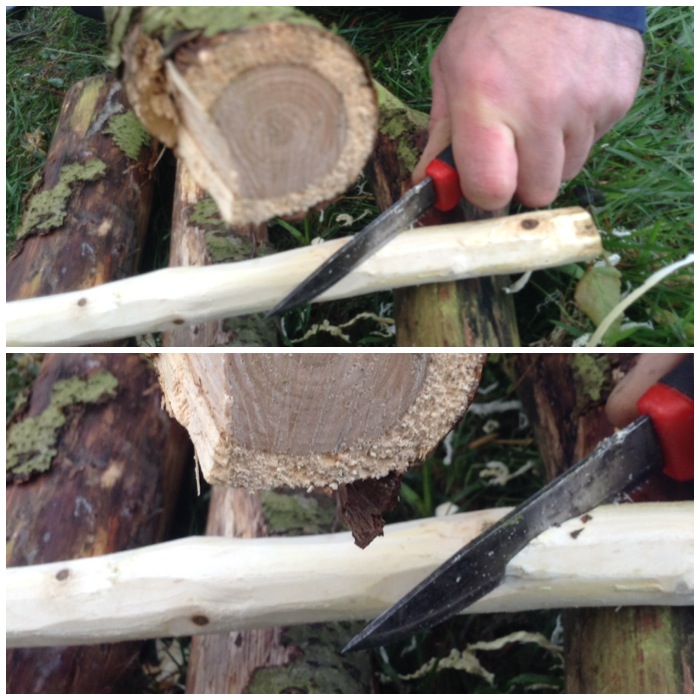
I then repeated the process for the other part of the X cut.
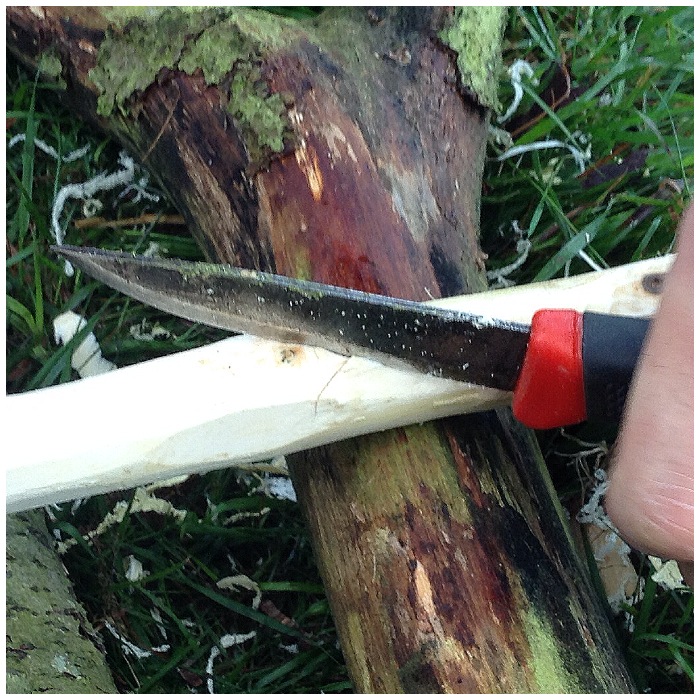
A simple X cut – this cut makes the carving of the adjusting hook much easier.
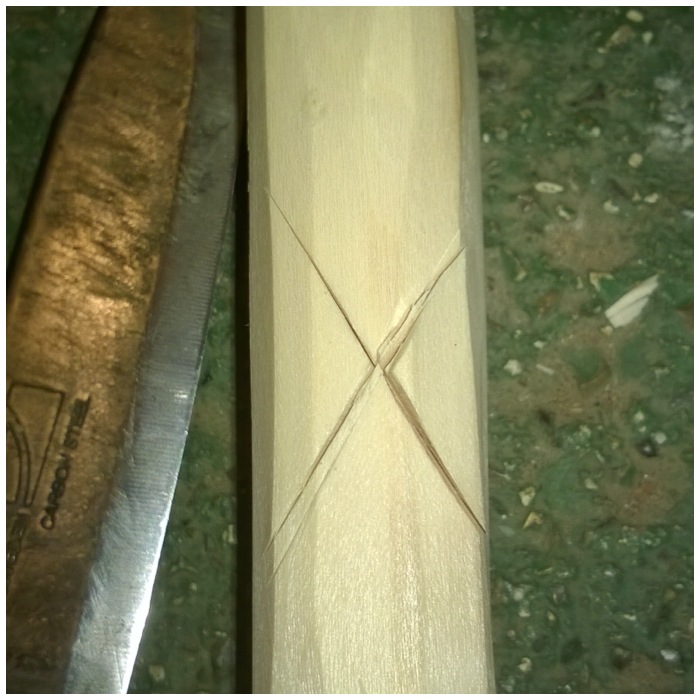
So that the pot hanger can hang properly you must remove the wood at the bottom of the X cut first (the bottom being the quarter of the X cut closest to the pot hook).
I use very fine cuts here and the original X cut acts as a stopper point so that you only cut away the wood that you need to.
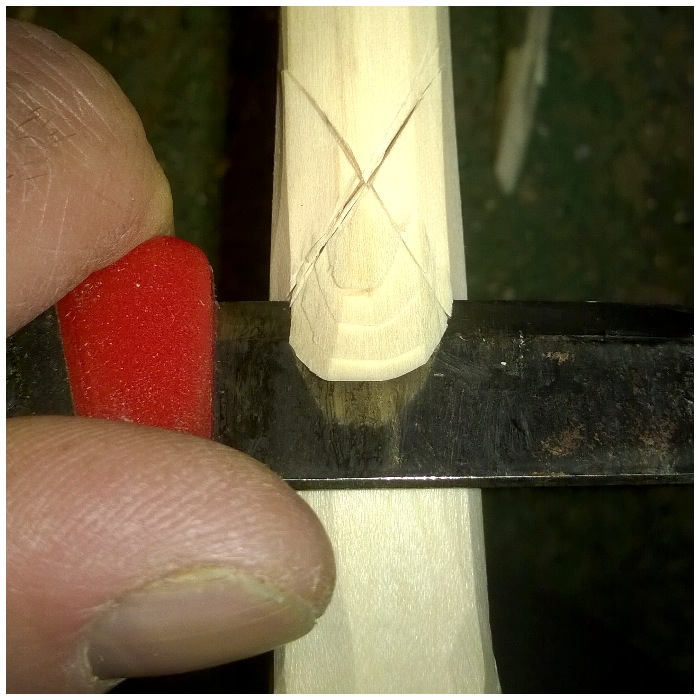
I normally remove a small area of wood just below the point of what will become the adjustable hook.
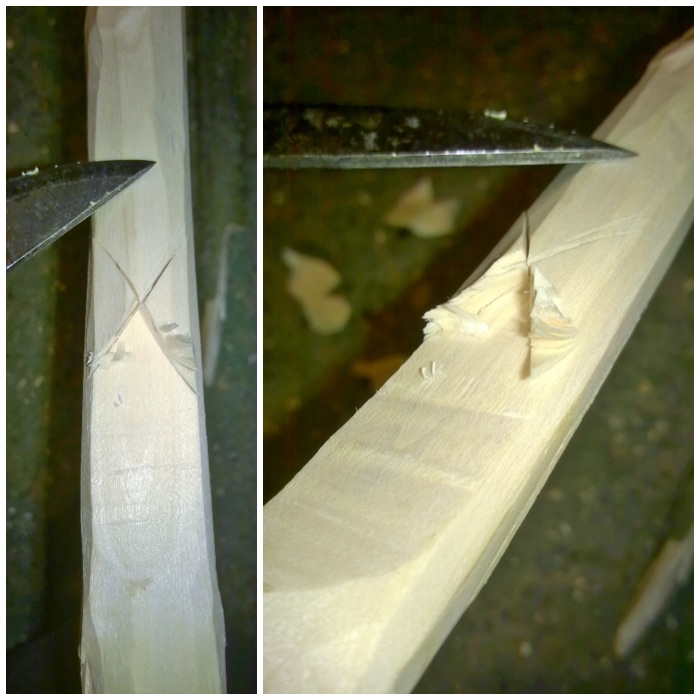
Once I’d removed the wood from the lower quarter I then removed the wood from one of the side quarters.
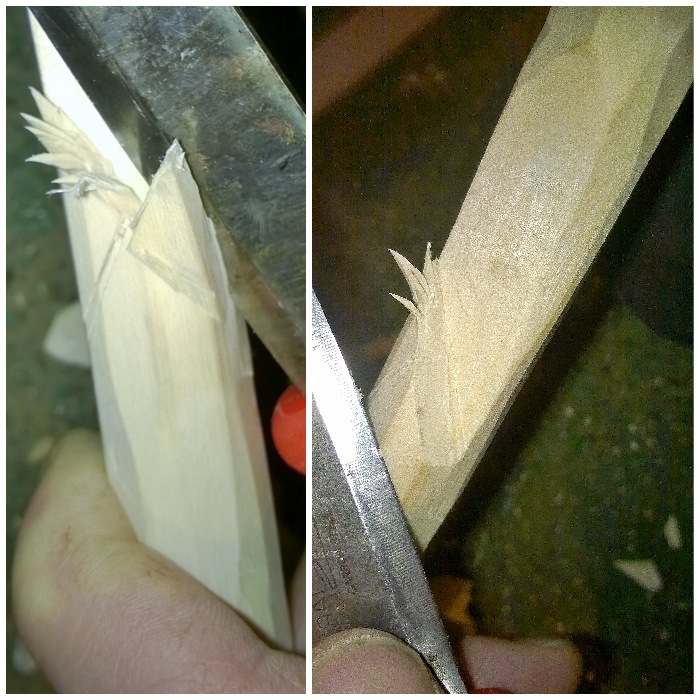
Then I removed the wood from the other side quarter leaving only the top quarter to act as the adjustable hook.
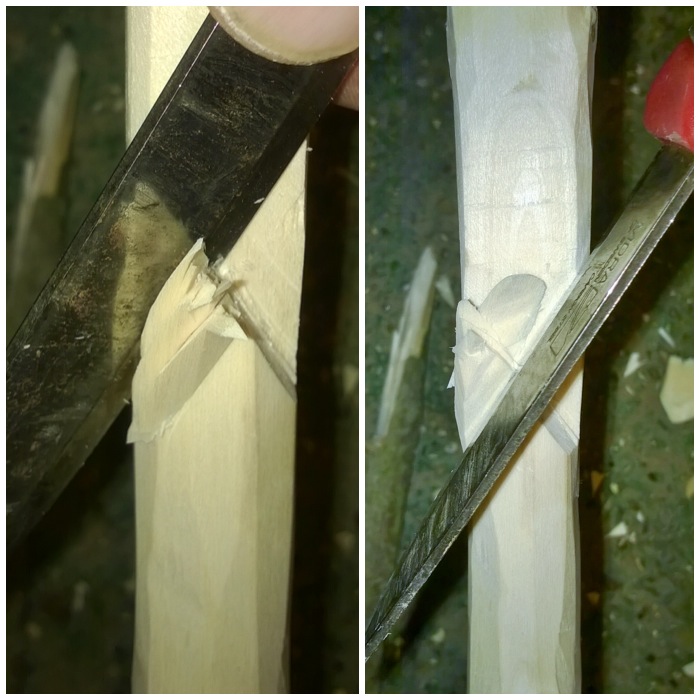
I kept carving down until I had exposed enough of the wood that I could carve out the final part of the adjustable hook.
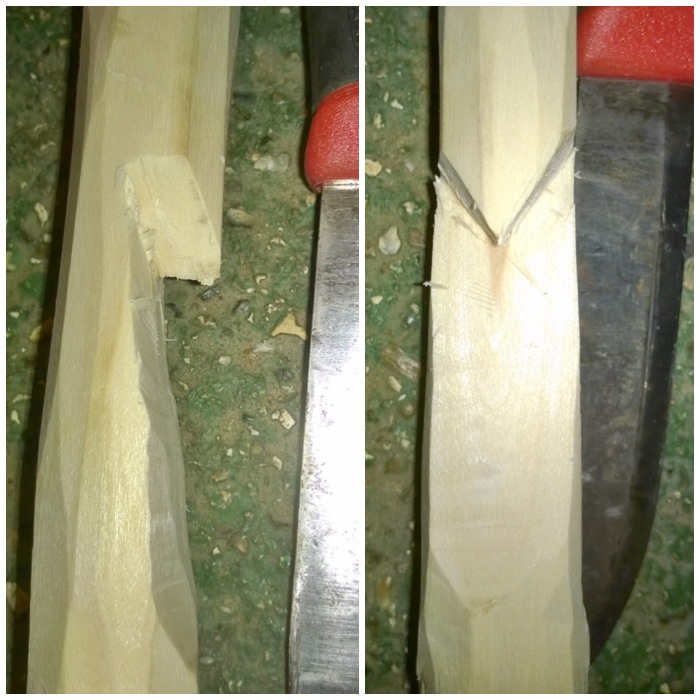
The final part I needed to do was to make an undercut below the point of the upper quarter. I kept reducing the wood until a nice point appeared.
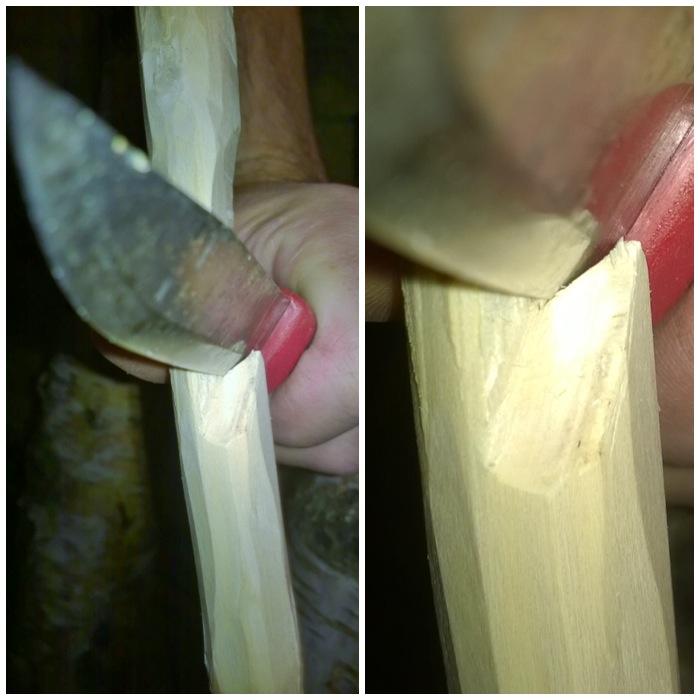
You can really see that undercut appearing in the picture below now. For safety I kept the pot hanger braced on the ground (a stump works as well) while I was carving it out.
For this pot hook I carved a further 2 hanging hooks along its length.
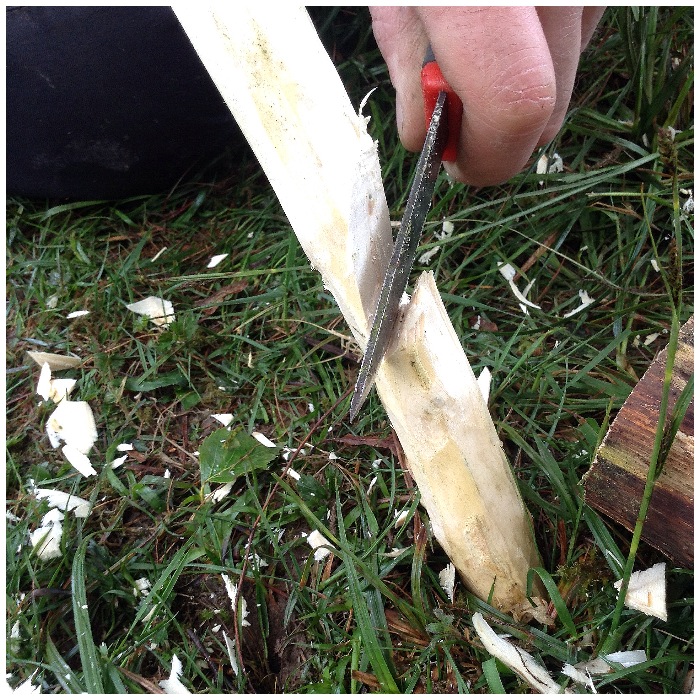
This is the final rough shape you are looking for. Any further carving or sanding would be purely for decoration only.
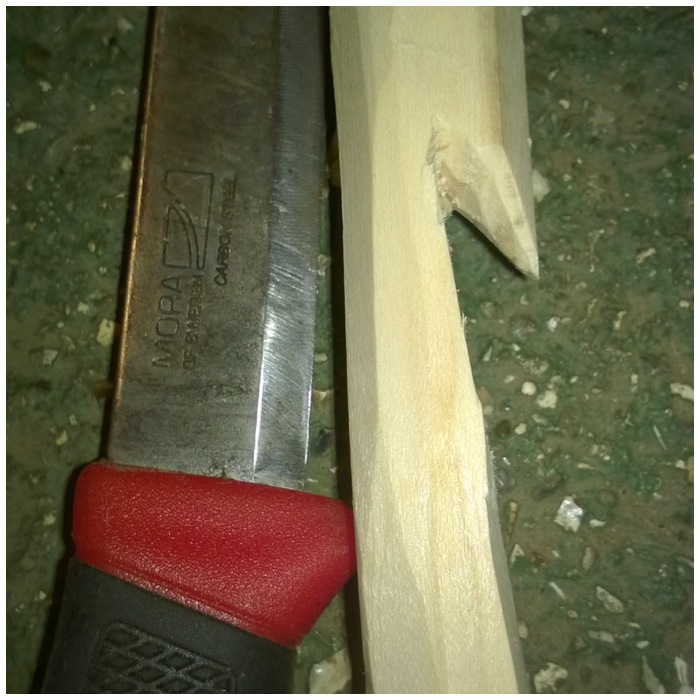
This pot hanger is particularly suited to the Wagon set up – Wagon (‘way gone’) coming as far as I know from the old tale that if you leave this set up standing when you leave your camp, it points the way for the naughty wood spirits to follow you 🙂
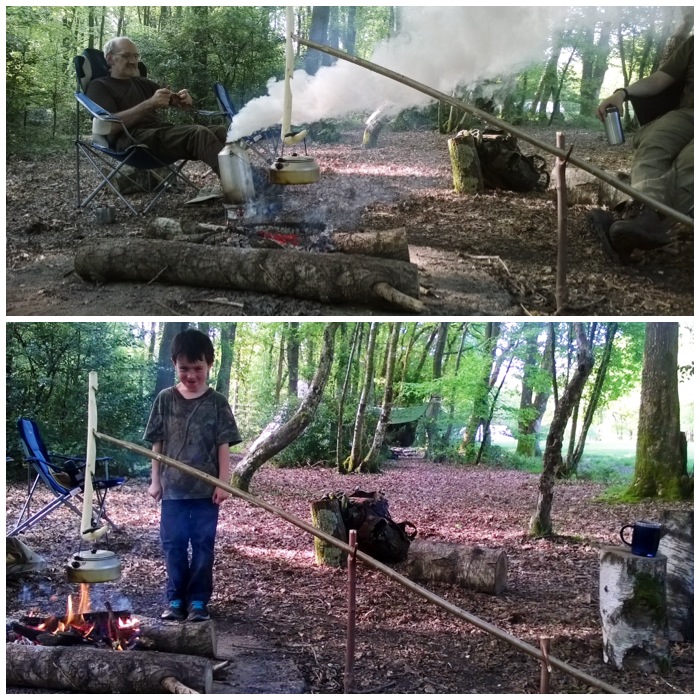
The hanging hooks attach to the Wagon stick by sitting in a small dimple on the end of it. In this set up I also used a forked stick to give the Wagon height and a smaller (Dead Man’s Finger) stick at the bottom of it to counterbalance everything.
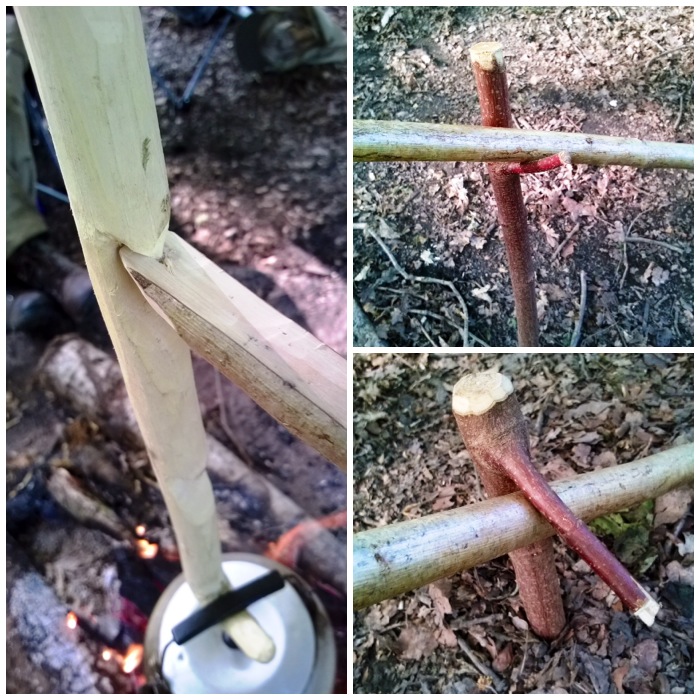
The whole set up is very easy to adjust for a fast or slow boil/cook.
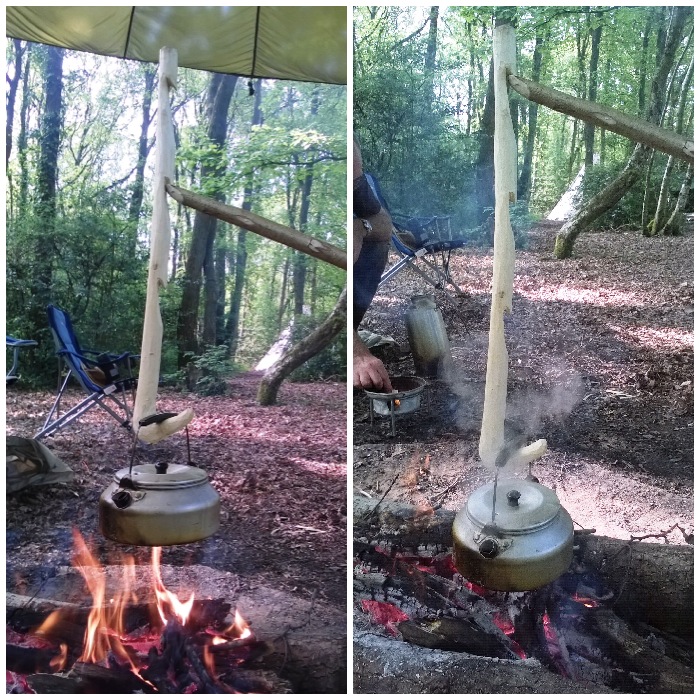
This is a great project for any bushcrafter to keep their hand in with simple carving techniques. It looks very simple at first but there are some tricky cuts that if you are not careful can cause a nick or two but the main benefit is – that the tea gets made.
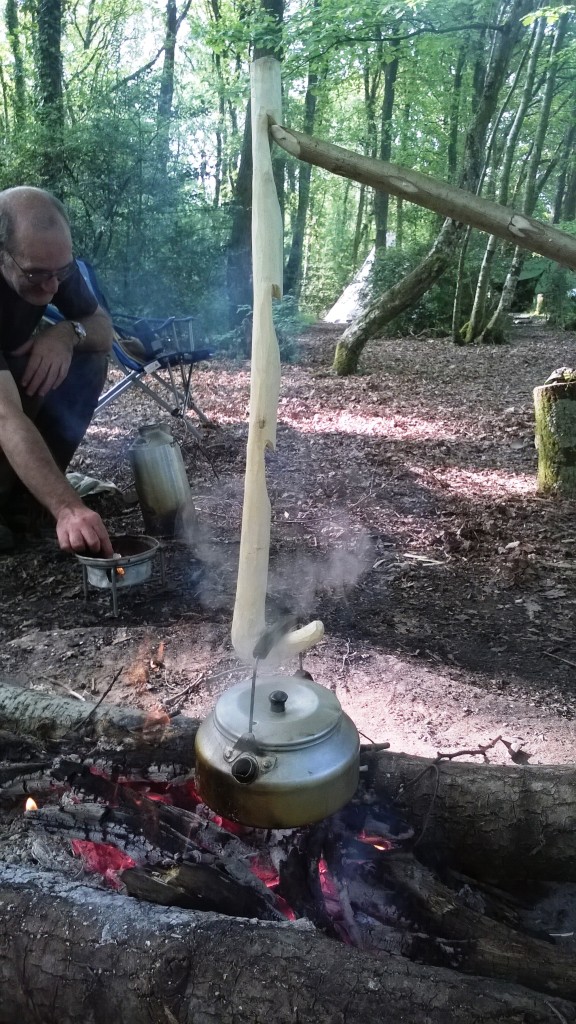
Cheers
George